Ground sensor applications has been particularly broad application of its model , different functions are also different, its main feature is the small size, easy toinstall, inexpensive , how do we determine what you want to do a proximity sensor to specifically look . First ,
the proximity sensor according to the measured object by selecting the material . If the required sensing distance is shorter , inductive proximity sensors can be easily and efficiently detect any type of metal objects. If the distance , you can use the photoelectric Camshaft Positioning Sensor. If the sensor is very far away , it is best to use on the radio or reflective photoelectric sensors. Secondly, since the capacitive proximity sensor can detect the material is very much, but the sensing distance corresponding to recently, and inductive proximity sensors similar . If you use a capacitiveCrankshaft Sensors , then the volume of the object to be detected can not be too small to meet the minimum sensing object of the sensor volume requirements. Ultrasound and diffuse proximity sensors can detect a wide range of materials , and detection distance is relatively long . However, in the detection of objects with irregular surfaces may cause problems . Finally , and more for the proximity sensor selection criteria , or to rely on the characteristics of the measured object , and to take
into account Crankshaft Positioning Sensor installation and environmental factors . Once all these issues are clear , then it can be selected from a number of sensors a suitable type. Understanding of the proximity sensor selection step that we can more quickly and accurately selected their own needs sensors. Of course, this is just a selection procedure , to treat specific problems but also specific coping
Camshaft position sensor, also known as the cylinder identification sensor, camshaft position sensors are generally expressed by CIS. Camshaft position sensor function is to collect the valve camshaft position signal, and input ECU, in order to identify the ECU compression TDC cylinder 1, thereby performing sequential fuel injection control, ignition timing control and knock control.
Cooling Temperature Sensor
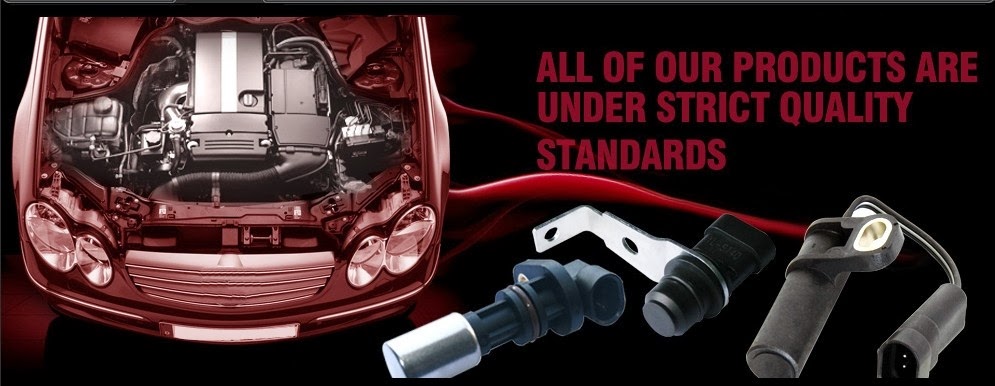
Cooling Temperature Sensor
2013年10月27日星期日
Proximity Sensor Selection Tips
Ground sensor applications has been particularly broad application of its model , different functions are also different, its main feature is the small size, easy to install, inexpensive , how do we determine what you want to do a proximity sensor to specifically look . First , the proximity sensor according to the measured object by selecting the material . If the required sensing distance is shorter , inductive proximity sensors can be easily and efficiently detect any type of metal objects. If the distance , you can use the photoelectric proximity sensors. If the sensor is very far away , it is best to use on the radio or reflective photoelectric sensors. Secondly, since the capacitive proximity sensor can detect the material is very much, but the sensing distance corresponding to recently, and inductive Camshaft Positioning Sensor similar . If you use a capacitive proximity sensor , then the volume of the object to be detected can not be too small to meet the minimum sensing object of the sensor volume requirements. Ultrasound and Engine Temperature Sensor can detect a wide range of materials , and detection distance is relatively long . However, in the detection of objectswith irregular surfaces may cause problems . Finally , and more for the Motor Temperature Sensor selection criteria , or to rely on the characteristics of the measured object , and to take into account the sensor installation and environmental factors . Once all these issues are clear , then it can be selected from a number of sensors a suitable type. Understanding of the proximity sensor selection step that we can more quickly and accurately selected their own
needs sensors. Of course, this is just a selection procedure , to treat specific problems but also specific coping .
needs sensors. Of course, this is just a selection procedure , to treat specific problems but also specific coping .
Embedded temperature sensor to continuously improve the quality of military equipment
With the continuous improvement of the quality of military equipment , micro- computers, electronic circuit system more and more used equipment and technology fields. Therefore weaponry on the ambient temperature requirements are increasingly demanding , especially in combat conditions, the ambient temperature directly affects the combat capability of weapons and even weapons for their own safety , as the sensor technology in military equipment on the application, this problem will be resolved using the temperature sensor . Embedded temperature sensor is a set of embedded technologies and intelligent sensor technology withintegrated temperature sensor , not only can be done by conventional sensors for measuring the temperature of the measurement , and can use computer technology to collect raw data for processing , with a small, processing speed, high intelligence and high degree of integration flower is the trend of modern sensor . Camshaft Positioning Sensor are generally composed of three parts : the unit under test , sensitive unit and a data acquisition unit. In fact sensitive unit and a data acquisition and processing unit is an integral part of the smart sensor , a temperature sensor is embedded in Motor Position Sensor based on the increased functionality. With computer technology, sensor technology , measurement and control technology as well as the continuous development of embedded technology , embedded Coolant Temperature Sensor in military equipment will be more widely on the application , which will bring the overall strength of our army a qualitative leap , so that army in modern warfare handy , to defend territory.
2013年10月24日星期四
How to install vibration velocity sensors
Speed sensor vibration velocity sensor , the vibration velocity is typically used to measure the vibration of the bearing , but there are a few cases in the shaft for measuring vibrations. How to install vibration velocity sensors do ? In the measurement of vibration velocity , if sensor is installed incorrectly or is not securely installed , the measurement results will cause distortion due to vibration or damage caused by the speed sensor . So we have to consider a good choice for vibration velocity sensor is installed. When the speed sensor is used to measure shaft vibration when installed in the field are usually taken with the hand , sticky water plasticine magnetic disk fixed , bolted in several ways . In the temporary vibration measurement , in most cases, hand sensors way , this method measured flexible , easy to use , especially when the number of the lack of vibrationEngine Coolant Temperature Sensor interchangeability bad, has a special advantage ; And this the disadvantage is that the test measurement error is relatively large, and the intensity of work is relatively large . Current speed sensor when measuring the vibration velocity , usually people will use the Engine Coolant Temp Sensor fixing screws directly on the bearing , not only can reliably measure the bearing at the top of the vibration in three directions , but also can be measured in two directions perpendicular to the plane of vibration this method is the best way to install the measure . Also has a different installation methods , due to the installation of the various conditions to determine that we have a good effect on manually installing a useful little plasticine paste the speed sensor is also more convenient , you need to note that plasticine vibration Motor sensor can not be pasted into the vertical plane , and can only be fixed on a horizontal surface , as affected by temperature adhesive force , high temperature and the lower the adhesive strength will be significantly reduced, so it is not suitable for fixing the high temperature high pressure turbine rotor and reel measuring wheel speed sensor bearing ; winter cold start , the bearing temperature is too low and it is not used . There is a similar permanent magnet sucker fixed speed sensor mounting , etc., when we observe the installation follow the rules is to measure the needs , the need to make sense of your environment changes , so that the vibration velocity sensor mounted only purpose is to more has the effect of reducing unnecessary errors
What are the application Humidity Sensor
Humidity sensor is able to feel the water vapor content in the gas and used to convert the output signal of the sensor. With the realization of modernization , it is difficult to find a field unrelated to the humidity , the humidity sensor for measuring or controlling the relative humidity of the gas or absolute humidity, dew point and so on. Can indirectly control the temperature . Below its typical application for an introduction. ( A ) in the humidity measurement system application ( a ) below 70 ℃ ( normally at -40 ℃ above ) , if relatively clean environment , the use of polymer sensors, polluting the use of Camshaft Position Sensor ( heating washing of regeneration type ) . Heating the cleaning process as it exists , can not be continuously measured , and the large energy consumption (1 ~ 10W). However, long life, use the optional heated sensor clean cycle is longer , such as chlorine oxy apatite Auto Temperature Sensor , 2 ~ 3 months wash , in addition, internal heat than the outer heat and low energy consumption . ( 2 ) In the range of 70 ~ 100 ℃ measured humidity , washing with a heating ceramic sensor , to improve the accuracy of linear and temperature compensation. In order to achieve more accuracy will have with the microcomputer. In hot and humid heat required frequent cleaning, such as more than 80% RH , the need to 30S cleansing once daily, preferably equipped with automatic cleaning device heating . ( 3 ) in the range of 100 ~ 150 ℃ humidity measured in the international community , mostly made of ceramicCooling Temperature Sensor temperature and humidity instrument . ( Two ) in the industrial automatic control application process in order to improve product quality and energy , usually in the product drying system , humidity control reactors , boilers, water vapor leak detection, integrated circuits or the head of the air-conditioning plant mostly using ceramic humidity sensor control ; variety of air conditioning systems, medical systems and humidity control can be polymeric or ceramic humidity sensor . ( Three ) in a steam leak detection systems used in thermal power stations , nuclear power plants, steam locomotives , boilers and other high temperature and pressure equipment , in order to prevent leakage, prevent accidents , humidity sensor can be used for leak detection . ( Four ) in the other systems used in home appliances dew condensation detection sensor can be used as tape recorders , car windows, condensation , frost detection. Humidity sensor applications driving the need for microelectronic circuit package failure mechanism analysis , due to IC failure and humidity have a great relationship .
How to correctly judge the photoelectric sensor output no signal
Photoelectric sensor is a photoelectric sensor element as a sensing element , widely used in the automation field . Photoelectric sensors for material handling, error detection , process manufacturing automation, object detection can also be used over long distances or fault is detected. Photoelectric sensors detect the distance of the object has a unique advantage , but in the specific use of the environment, there will be some technical problems , which we need methodical technical judgment. In the application of photoelectric sensors to detect objects in the distance , a lot of users will encounter problems when using photoelectric sensors to detect objects is no output signal after , making it impossible for subsequent data analysis. Most people see no signal sensor output may often be some wrong judgment , such as some people on the direct determination of Shaft Position Sensor bad reason. But the reason is not all like that, photoelectric sensor detects an object after no output , there may be many reasons , we need to do it step by step investigation . The first thing to consider is wiring or configuration problems . For beam photoelectric sensor must be cast by the light unit and a light unit used in combination with both ends requires power ; while retroreflective Engine Temperature Sensor probe and must be retroreflective sheeting used in combination ; same time, the user must provide a stable power supply to the sensor , if it is DC power supply , you must confirm the positive and negative , should the positive and negative connection error will cause the output signal is not . The reason analysis is to consider Camshaft Position Sensor itself , we also need to consider the problem is to detect the location of objects , if the detected object is not in the detection area , so that the detection is futile. Test object must be detected in the sensor area , that is, can sense the optical range. Secondly, we must consider the optical axis of the sensor there is no alignment problem , on the radio type of light-emitting portion and a light receiving unit must be aligned with the optical axis , the corresponding portion of the retroreflective type sensor must be aligned with the optical axis and the reflector . The same should also consider whether the detected object is the standard sensing object or minimum standard sensing object , object detection can not detect an object less than the minimum standard , thus avoiding lead shot , reflective not well detect transparent objects , like a reflection on detecting the color of objects is required, the deeper the color , the more recent detection distance . If the above conditions can be excluded to make it clear , we need to do is to detect environmental disturbances . Such as light intensity can not exceed the rated range ; if there is dust environment of the scene , we need our regular cleaning optical sensor probe surface ; or more sensors close fitting , mutual interference ; there is a relatively large impact that electrical interference , if surrounded power equipment , interference must have the appropriate anti-jamming measures . If you have done the above one by one investigation , these factors can be explicitly excluded or no signal output , it is recommended to return factory testing to determine .
The method of pressure sensors to achieve impact
Pressure sensors used in many bad environment , some of the bad environment may be more severe , such as pressure sensors need to measure the impact pressure , the measured impact pressure generally requires relatively high pressure sensor performance , we usually have several ways to measure the impact type pressure . The first method is to change the pressure transmitter chip , not an ordinary ceramic cores or diffused silicon core , but with strain gages , strain gauges is a strain on the DUT will be converted into an electrical signal of change sensitive device. It is a piezoresistive Camshaft Position Sensor of the main components . Resistance strain gauge is the most widely used metal resistance strain gauges and semiconductor strain gauges two kinds . Metal resistance strain gauges have filamentous strain gauge and the metal foil strain gages two kinds . The strain gauge is usually via a special adhesive binder tight mechanical strain is generated on the substrate , the force occurs when the substrate stress , the resistance strain gauge is generated with deformation, the resistance strain gauge is changed , so that the the voltage across the resistor changes . The strain gauge force generated when the change in resistance is usually small , it typically are composed of strain gage bridge , and through subsequent instrumentation amplifier is amplified , and then transmitted to the processing circuit . Strain gauge Auto Temperature Sensoris generally shock and impact resistance is better, but this sensor accuracy with their manufacturers . The second method is to use an ordinary ceramic Coolant Temperature Sensor or pressure sensor to measure diffusion silicon , but not be measured directly , but with the addition of a buffer tube , which also can measure the impact pressure . This method is economical , easy to install , so the application is very extensive. Regardless of the method is to measure the impact pressure sensor core body protection is not strong pressure washed out . Which method based on the specific use now have a bad environment and customer choice .
A brief description of the flange torque sensor
Torque sensor in various industries have a wide range of applications, widely used in motors , generators, gear, engine torque, speed and power testing. We all know that the torque sensor can generally be divided into static and dynamic torque sensor torque sensor , which is from the torque sensor measurement to points, from the torque sensor structure can be divided into flange torque sensors and illegal orchid torque sensors , torque flange which sensors can be divided into single and double flange flange torque sensor torque sensor . Single flange torque sensor suggests that it is the end of the torque sensor with flange -type structure , so easy to install and fixed sensors , single flange design is more convenient for on-site installation, ideal for static , non- continuous rotation torque force value measurements. Learn the single flange torque sensor on a good understanding of double flange torque Camshaft Position Sensor , torque sensors dual flange torque sensor is based on a single flange adds a flange structure , ie the torque sensor flange structure at both ends . Double flange torque sensors and single flange Auto Temperature Sensor as generally only suitable for static , non- continuous rotation torque force value measurements. Understanding of the structure ofAutomotive Temperature Sensors can be a good choice for our torque sensor , such as measuring the dynamic torque sensor flange structure we are not going to choose a torque sensor , select Static torque sensor go to consider when selecting a single flange or torque sensor double flange torque sensor , so that we can narrow our choices , better and faster we choose the suitable torque sensor .
2013年10月20日星期日
Unique advantages photoelectric sensor
Photoelectric sensor applications more monitoring, response systems. Large aerospace military field , small -car electronic eye , etc., can be applied photoelectric sensors. In many industrial production line there are some application cases. For example, electronic eyes monitoring , digital rangefinder and counting ! Here to introduce you to the unique advantages of photoelectric sensors under what . 1 ) If long distance detection is retained on the radio more than 10m detection distance , etc., will be able to achieve other detection methods ( magnetic , ultrasonic , etc. ) can not be away from the detector . 2 ) restrictions on the detection of small objects caused due to the detected object shading and reflection for the detection principle , it is not like the proximity sensor will detect metal objects limited , it may be on the glass . Plastics timber of liquid , almost all objects detected . 3 ) Response time is short for high-speed light itself , and Crankshaft Positioning Sensor circuit constituted by the electronic components , it does not include mechanical working time , the response time is very short . 4 ) High resolution through advanced design techniques make the light beam is concentrated in a small spot , or by constructing a special light-receiving optical system to achieve high resolution . Small objects can also be detected and the position detection precision . 5 ) non-contact detection can be achieved without mechanical contact with can detect objects to achieve detection , it will not detect the object and sensor damage. Therefore, Car Temperature Sensor can be long-term use . 6 ) can be achieved by detecting the object forming the color determination of the light reflectivity and absorption of the light according to wavelength of light to be cast and the detected object color combinations vary . By utilizing this property , can detect the color of objects detected. 7 ) to facilitate adjustment of the projection type, visible light , flood light beams are visible to the eye , to facilitate adjustment of the position of the detected object .
Displacement sensor parameters
Displacement sensor parameters - displacement sensor is a relatively common sensors, displacement sensors is it ? Displacement sensor parameters What ? Displacement sensor , also known as linear sensor , it is divided into inductive displacement sensors , capacitive displacement sensor , optical displacement sensors , displacement sensors ultrasonic displacement sensors , hall-type displacement sensor . Inductive Coolant Temperature Sensor is a linear device belonging to metal induction , after power sensing face of the switch will generate an alternating magnetic field , when a metal object close to this sensor surface, the metal is generated eddy current draws oscillator the energy, so that the oscillator output amplitude linear attenuation , and then the change in the amount of attenuation to accomplish the purpose of non-contact sensing object . Main parameters Nominal resistance: potentiometer resistance indicated above . Repeatability: This parameter is as small as possible . Resolution: minimum displacement sensor displacement values can feedback This parameter smaller the better. Conductive plastic Coolant Temperature Sensor resolution is infinitesimal . Permissible error: nominal resistance and actual resistance the difference with the percentage of the ratio of nominal resistance , said resistance deviation , which represents the precision potentiometer . General tolerances within ± 20% as long as it meets the requirements, because the general displacement sensor based on the partial pressure of ways to use the specific resistance of the size of the sensor data acquisition is not affected. Linearity: Linearity error This parameter is smaller and more good life: conductive plastic displacement sensor in 200 million times.
Sensors monitor the gas burner in the family of Application
Among the families of sensors are used with a temperature sensor , gas sensor , optical sensor , an ultrasonic sensor and an infrared sensor , etc. . Wherein the temperature sensor is the most common applications in the appliance , it is not only to bring to life a great convenience , but also to avoid fire , damage and other unexpected events. Recently published in the EU energy saving regulations , found that the use of new sensors control the burner , as many manufacturers of heating equipment upgrade of choice. Here's Crankshaft Positioning Sensorin the home under surveillance gas burning application . First, the gas and air mixture prior to combustion detection temperature , flow rate and composition of the combustible gas , so that the appliance can be calculated and the required heat supply air . Second, to detect possible reaction zone. Ions and some no-load number of atoms in the reaction can occur given product number . For example , if you know the volume fraction of oxygen , it is possible to infer the need to adjust the supply of gas or air . Third, the combustion state by detecting the carbon dioxide gas , carbon monoxide and nitrogen gas quantity and then OK. Being selected probe changes and changes in combustion characteristics of the relationship , thereby establishing a reliable control system. With the smart home slowly into family life , Car Temperature Sensor will need to be applied more and more , which is now a major sensor manufacturers in emerging markets . Vigorously develop the domestic sensors, to further improve the human home life, improve quality of life and taste , which is sensor manufacturers contribution to society .
A temperature sensor for detecting the temperature
Temperature sensors of various physical properties of the use of material with the temperature variation of the temperature sensor is converted to electricity . Temperature sensor is a core part of the temperature measuring instruments , a wide variety . Press the measurement can be divided into contact and non -contact two categories, in accordance with the characteristics of Cooling Temperature Sensor materials and electronic components are divided into two types of RTD and thermocouple . Temperature sensor is used to monitor the main machine which compensates for temperature or the temperature overheating protection, which in the working machine as the motor rotation and the movement of moving parts , the cutting generates heat , but the temperature distribution is uneven, will cause certain temperature , the thermal deformation of CNC machine tools , precision machined parts affected . To avoid these effects, Crankshaft Positioning Sensor will be installed on the machine , it can be detected that the real temperature value transmitted to the control system , the set point can be reached at the time to the control system of the machine temperature can be monitored and control .
A pressure sensor for detecting the pressure
Pressure sensors are most commonly used in industrial practice of a sensor , which are widely used in various industrial automation environment, involving water utilities , rail transportation, intelligent buildings, production automation , aerospace , military, petrochemical, oil, electric power, shipbuilding , machine tools , pipes and many other industries. The pressure Motor sensor is a Crankshaft Positioning Sensor is converted to an electrical signal on the machine, the machine adapted clamping force on the workpiece is monitored when the clamping force is lower than the set value when the work will lead to loose , the system sends an alarm , stop take the knife ; additional tools can detect changes in the cutting force . Moreover, it is in the lubrication system, hydraulic system , pneumatic system, for detecting the passage or the gas pressure in the oil or gas when the pressure is less than set when the set value , the shock will be activated and then sends signals to the control system to control it.
2013年10月17日星期四
Fire gas sensor is booming
Sensor technology in the fire , the fire gas sensor technology started late, but rapid development , especially in the field of early fire alarm fires become more and more attention of researchers and has developed various types of fire, gas sensors and smart , composite gas Shaft Position Sensor. Currently, the fire continues to move gas sensor miniaturization , intelligent and multi-parameter , multi- criteria composite probing direction. With the new sensor technology and application of new materials and the development of microelectronics technology , fire, gas sensors becoming smaller , miniaturization . Resistance using nanoparticles composed of gas with the surrounding environment changes and changes in the characteristics of nanomaterials can be made Crankshaft Position Sensor, toxic gases, flammable gas detection and quantitative measurement . Because nanomaterials crystal surface catalytic activity, as well as having a porous structure and other characteristics , the use of nano- crystalline film produced gas sensor has more choice and anti-interference, improving the accuracy of the fire alarm to reduce false positives. Meanwhile, the small size of nanomaterials , surface area is small , greatly reducing temperature , reducing power consumption, so that the fire gradually sophisticated gas sensor miniaturization Yin Nami , film and other new materials preparation technology successful application of integrated fire and gas sensors intelligence provides a good prerequisite. Automotive Temperature Sensorswill make full use of micromechanical and microelectronic technology, computer technology , signal processing technology, circuits and systems , sensor technology, bionics , neural networks, fuzzy theory and other subjects on the basis of integrated technology to develop. Able to simultaneously monitor multiple gas developed automatic intelligent digital Sensor Camshaft , will be the next major development in this field . Fire is an extremely complex physical and chemical processes in different environments and different resultant fires burning material , such as gas composition , smoke particle size , temperature distribution and spectral composition are different , only one fire detection parameters vagaries the various types of fire is bound to have great difficulty , it may cause a false positive signal non-fire dust , water, gas , smoke, etc. do not have the real fire parameters . Therefore, multi-parameter , multi- composite fire detection criterion can not only overcome the single fire caused by false positives parameter , you can also identify the non-fire signaling leads to false positives , the future is still hot fire gas sensors . In addition, multi-parameter , multi- criterion composite gas fire detection sensor also allows to reduce the time to achieve early warning .
Thin-film temperature sensor case studies
Film temperature sensor is a new type of temperature sensor , working principle and common thermal resistance, thermocouple the same , but it's hot junction thickness of only a few microns . Film Camshaft Position Sensor because of its small , short response time , high sensitivity, ease of integration , etc., suitable for measuring rapid changes in body temperature over time . Film thermocouple principle was first used by the Germans during the First World War made P.Hackmann and developed a film thickness of only 2um thermocouple sensor for measuring bore bullet shot in the foot after a temperature change . Many scholars from around the world followed the film temperature sensor structure , method of preparation , performance and prospects a lot of research work , and has made encouraging progress in recent years, is widely used in internal combustion piston top surface of the combustion chamber wall and cutting tips and other transient temperature tests . Domestic Northwestern Polytechnical University, Li Fu-Guo Huang Lu , who developed a new right to film thermocouple Camshaft Positioning Sensor for measuring the work surface and the internal die temperature transients ; Xi'an Highway University, developed a money orchids, wall heat transfer for internal combustion engines process analysis of the film Cooling Temperature Sensor ; Dalian University of Technology precision & processing , Ministry of Education key Laboratory of Bao yuan et al study and produce for measuring cutting temperature NiCr / NiSi film thermocouples. Developed film temperature sensor is the key to solve the coating resistant , solid , impact and insulating layer between the issues and the difficulty of combining domestic and foreign scholars have done a lot of research on the coating process and produce the corresponding thin film sensors. So far, the researchers have developed a thin-film temperature sensor can be well applied in some situations , but its versatility deficiencies , and the cost is high ; simultaneously by technology and material constraints , sensor life are generally more shorter.
Affect the development of the four load cell competition in the industry
Weighing sensors with other sensors industries there is a fierce competition that has the image of brands, services and other civilized gentleman of the dispute , but also change the material for components, spell cost , disposable quality unscrupulous unfair price competition. The competition is mainly the following four points : 1, the price of some electronic weighing products is extremely low , some only one-tenth of the international market price , this factor determines the load cell is no room for maneuver on pricing , forcing production enterprises reducing their quotations and offers many free services , or forcing producers to maintain inventory levels , bear the risk and cost of inventories , the production company profits is therefore reduced ; 2 , misleading consumers, so many users have misunderstood the load cell stability and reliability targets. Some companies are semi-permanent part of the product , are IP67, IP68 sealing level of product protection can be stabilized for ten years at least mention , but will say that this was the vulnerability of the device under load frequently , allowing the user to accept this Shaft Position Sensor prices also accept quality of this product ; 3 , at the expense of product quality for the price , crazy reduce costs, using a variety of means to seize the market , for example, $ 3,000 per tonne instead of one million yuan 40Cr steel the 40CrNiMoA alloy steel load cell elastomer to do with about $ 5 instead of an ordinary strain gauge precision strain Crankshaft Position Sensor to do , without the formation of low-quality low-cost, make a profit ; 4 , lax management and supervision of legal metrology so that some of the production equipment is poor or lacking in personal and corporate load cell is relatively easy to enter the industry , leading to increase productivity and drive down prices, making formal corporate profits dropped significantly , and even non-profit discontinued , difficult. These victims are often Crankcase Position Sensor level of technology , process equipment is good, strict quality control , good after-sales service load cell business, the ultimate victims are the majority of users . On the surface, the price war in recent years is the direct cause of the load cell market crowded, some people and companies in order to profit , survival waged a last resort , and its essence is about leadership and management oversight authority , leadership and management control, supervision and inspection caused by lax .
Further accelerate the pace of intelligent sensors
Today, integrated smart sensor technology has made remarkable development , and domestic sensors have gradually opened up the field of smart sensor market . Now our high-performance multi- sensor micro-controller , along with digital and analog two kinds of output, and the specific requirements for some users , in the original products based on secondary development , and require a very short period , reaching the purpose for the user to save time , but also greatly improving efficiency. Has been widely applied to a variety of fine fields. Insiders said about the future , we can just move a finger, can only via mobile phone or computer and other electronic products can be realized on the control of household goods , to achieve truly automated home , while also through a variety of agricultural products,Crankshaft Position Sensortimely monitoring, for example, to effectively carry out irrigation and spraying , etc., in order to reduce costs and improve earnings. In addition , you can also wear a Camshaft Position Sensor body health data collection, protect people timely understanding of their own health . With intelligent Crankshaft Positioning Sensor , will people's lives changed dramatically , and can be widely applied to the sensor field , such as smart logistics, smart healthcare , smart home , intelligent transportation , industrial automation , environmental protection, financial services industry , fine agriculture, national defense and military , networking , and other areas was smart sensor provides a great market space for development .
Oxygen sensor works
Fast development of the automotive industry , automotive replacement is getting faster and faster , increasing the level of automobile manufacturing technology , more and more precision machining parts for automotive emissions requirements become more stringent , the Camshaft Position Sensor in the middle of vulnerable the impact of fuel combustion , the fuel quality requirements are also increasing. Oxygen sensors are used in automotive engine management system, by detecting the oxygen content in the exhaust gas , the probe results in the form of feedback signals to the engine management system, the detection results and the exhaust gas oxygen content was one relationship , the engine management system according to the feedback signal after calculation , analysis and judgment to issue directives to the actuator to complete a variety of actions , so that the engine can be in a variety of working conditions in order to work optimally . Sensor works: oxygen sensor sensitive components using its ceramic zirconia ceramic materials at high temperatures characteristic of oxygen pump oxygen sensing signal . Zirconia ceramic at a temperature and oxygen ions may be turned on , when the oxygen concentration on both sides there is a difference , will be based on the Nernst equation potential difference is generated . Air-fuel ratio when the engine is operating in the vicinity of λ = 1 (typically λ = 0.99-1.01), zirconium oxide ceramic will exhibit a significant change in the electric potential difference , therefore , the Engine Temp Sensorof this step- by sensing the change in the electric potential of the work of the engine the feedback control , which enters the engine when the oxygen-depleted or enriched provide basic response signal , indicating the engine air-fuel ratio control system will be adjusted to standard conditions . Cars generally need to install two oxygen sensors , catalytic systems were installed in the front and rear . Catalytic system is attached to the tip of the oxygen sensor for detecting oxygen concentration in exhaust gas , according to the level of oxygen concentration in the exhaust gas back to the gasoline engine , the gasoline engine according to Coolant Temperature Sensor feedback signal increases or decreases the air-fuel ratio , so that air-fuel ratio always in perfect combustion state λ = 1 nearby. Catalytic exhaust system of harmful gases such as CO, CH and NOx , etc. into harmless carbon dioxide, water and nitrogen , and finally confirmed through an exhaust gas oxygen sensor has been transformed completely .
Principle and Application of Gas Sensors
The so-called gas sensor is used to detect whether a certain area in the presence of a specific gas and / or capable of continuous measurement of gas component concentration of the instrument. In the coal mine , petroleum, chemical , municipal , medical , transportation , family and other security aspects , commonly used in the detection of combustible gas sensor , combustible , toxic gases or existence , or oxygen consumption and so on. In the electric power industry and other manufacturing fields, but also quantitative measurement of flue gas sensor used in the concentration of each component to determine the combustion of harmful gas emissions and the like. Field of environmental monitoring in the atmosphere , the use ofCrankshaft Position Sensor determine environmental pollution situation , it is very common. Classification of gas sensors from detecting the type of gas , the often divided into combustible gas sensor ( often using catalytic combustion , infrared, thermal conductivity , semiconductor type ) , toxic gas sensors ( generally using electrochemical , metal-semiconductor , photoionization , flame ionization type ), hazardous gas sensor ( often with infrared , ultraviolet , etc. ) , oxygen ( often using paramagnetic , zirconia ) and other Engine Coolant Temperature Sensor ; from the use of the instrument , into the portable and stationary ; obtained from the gas the way the sample is divided into diffuse ( i.e. sensor mounted directly on the object to be measured environment , the measured gas through natural diffusion in direct contact with Car Temperature Sensor element ) , suction ( suction pump is through the use of other means , to be tested gas is introduced into the sensor sensing element detection. based on the measured gas is diluted , can be subdivided into full suction and dilution type, etc. ) ; from the analysis of gaseous components , and is divided into a single formula ( only for specific gas detection ) and compound of formula ( composition for simultaneous detection of multiple gases ) ; press Sensor detection principle , be divided into thermal , electrochemical , magnetic , optical , semiconductor type , such as gas chromatography type .
Sensors on the device application in life
Appliance industry has been a hot industry , now more or less every
household has a certain number of home appliances , we can say all of
the appliances in both sensor applications, sensor devices are
appliances must . People want to enjoy intelligent life, then smart
appliances is definitely an important part , and the various types of
sensors has become an important component of intelligent appliances .
More and more vendors starting to focus Shaft Position Sensor
technology in the home appliance products in the application , and
actively promote such applications to meet the needs of consumers and
enhance the user experience. In order to improve the safety performance
of appliances , sensors are widely used, except in the rice cooker
applications, also used in induction cooker and so on. The infrared Engine Coolant Temperature Sensor
used in cooker , you can make sure no one stops cooking fried foods, or
high-temperature reminder to further enhance security. In energy
conservation, green low popular now , appliances save energy also become
manufacturers and consumers attention. Relying on lower power rating
values to achieve the energy saving effect of the " hard energy"
traditional way, consumers can not meet the application requirements, so
the use of sensors to achieve the user to control the use of "soft
energy" gradually born. If the air conditioning indoor unit is equipped
with the infrared sensor , to obtain the interior region 752 of the
thermal image , to analyze the position of the body , the body activity,
floor / wall / ceiling / window position information and the room
layout . According to the different areas where the person to adjust the
temperature , and the remote control to emit energy saving tips and so
on. Engine Water Temperature Sensor
is widely used at present in the refrigerator , the refrigerator door
switch to detect the state and frequency. And according to the user 's
habits and trends to achieve the cooling suit every home run . Depending
on the frequency of use to adjust the refrigerator and freezer for
cooling , to meet the needs of user applications and also save energy.
The foreseeable future sensor applications in white goods will be more,
and achieve different new features. Sensors on the device in life will
be more widely applied , with the development of sensors , appliances
will be more intelligent, not only to avoid security risks but also to
enable people to enjoy a comfortable life.
In the course of the humidity sensor has several issues deserve attention
In the course of the humidity sensor has the :Select the measurement range and weight, temperature , the choice of the humidity sensor must first determine the range of measurement. In addition to weather , research departments, to engage in temperature and humidity monitoring in general do not need all wet process (0-100% RH) measurements. In today's information age , Shaft Position Sensor technology and computer technology , automatic control technology closely integrated with . The purpose is to control measurement , measurement range and control of the use of collectively . Of course, do not need to engage in monitoring and control system applications are concerned, directly select universal moisture meter on it. Select the same measurement accuracy and measurement range , measurement accuracy of the sensor with the most important indicators. Each increase - percentage points. It is for the sensor to a higher level , or even on the next level . To achieve different accuracy because its manufacturing costs vary widely , the price is also very different. For example imports an inexpensive Engine Coolant Temperature Sensor only a few dollars, and one for the entire wet process of calibration and humidity sensors to a few hundred dollars , a difference of nearly a hundred times . Therefore, the user must be tailored , not the blind pursuit of "high, fine, sharp ." Manufacturers often give its humidity sensor segmentation accuracy . In case of low humidity segment ( 0 a 80% RH) was ± 2% RH, and the humidity segment (80-100% RH) was ± 4% RH. And this accuracy is at a specified temperature (such as 25 ℃) value. If used at different temperatures andCar Temperature Sensor. Its indication should also consider the impact of temperature drift . Is known , the relative humidity is a function of temperature , temperature seriously affecting the relative humidity within the specified space . Each change of temperature 0.1 ℃. Will generate 0.5% RH humidity change (error ) . If it is difficult to do using the occasion thermostat , the proposed high measuring precision is inappropriate. Because humidity variations with temperature drift suddenly uncertain , then talk about measuring precision will be moot . So first of all to control humidity temperature control is good , this is the large number of applications are often temperature and humidity - sensor integration and not simply because of the humidity sensor . In most cases, if there is no precise temperature control means , or a non- sealed space is measured , ± 5% RH of accuracy is sufficient . For applications requiring precise control of temperature and humidity of the local space , or need to keep track of changes in humidity recording of the occasion, and then use ± 3% RH. Above precision humidity sensor . And this corresponds to the temperature sensor. Its measurement accuracy ± 0.3 ℃ above shall be sufficient , at least ± 0.5 ℃ for . The accuracy better than ± 2% RH sensor calibration requirements but even the standard humidity generator is also difficult to do , not to mention the sensor itself .
Regardless of the vibration sensor is in the application of the test or have a key role
Regardless of the vibration sensor is in the application of the test or have a key role is an electromechanical conversion unit , we sometimes also called the vibration sensor transducer, the vibration pickup . The vibration sensor is not directly the original volume to be measured into a mechanical energy , but the original mechanical quantity to be measured as a vibration Automobile Temperature Sensor input, and receiving section to be received by the machine , form another for converting a mechanical quantity , and then finally by the electromechanical conversion section converts electricity . Therefore, performance of a sensor receiving portion by the mechanical and electrical converting portion determined performance . 1 , the relative mechanical principle due to mechanical movement is receiving physical movement simplest form , so people first thought is to use mechanical methods to measure vibration, thereby creating a mechanical vibrometer . The mechanical Motor Sensors receiver is built on the basis of this principle on . Relative type vibrometer working principle is the measurement receiver , the instrument does not move in a fixed bracket, make contact with the measured object vibrating rod in the same direction , and by the elastic force of the spring in contact with the surface of the measured object , when the object vibrates, the antenna rod to follow it with the movement , and to promote the movement of the tape recording pen depicted on the vibration displacement of the object with time variation curve can be calculated according to the recording of the displacement curve of the size and frequency parameters . 2 , the principle of inertia mechanical inertia receiving mechanical vibration vibrometer when vibrometer is directly fixed to the measured vibration measuring point on the object , when the measured vibration Engine Water Temperature Sensor housing with the movement of objects , by the elastic support of inertia mass relative motion to the housing , is mounted on the block and to record the recording pen can be mass element and the shell relative vibration displacement amplitude , and the use of inertial mass and the housing relative to the vibration displacement relationship can calculated absolute vibration measured object displacement waveforms . 3, the vibration sensor is an electromechanical conversion general principle , the vibration sensor to receive the mechanical principle , only the relative type, inertia type two, but in the electromechanical conversion , due to the different nature of the transformation methods and its wide range of application is extremely extensive. In modern vibration measurement sensors used , is not the traditional concept of separate mechanical measuring device , it is only the entire measurement system in a part of , and with the subsequent electronics are closely related. Since Camshaft Position Sensor different internal electromechanical transformation principle , the output power is also different . Some of the changes in the amount converted into mechanical force , the charge changes , some changes in the mechanical vibration is converted into resistors, inductors and other electrical parameters changes. Generally , the charge and can not be directly subsequent display, recording , analysis instruments accepted . Therefore, electromechanical transformation principle for different sensors must be accompanied by specially equipped measuring circuit . Measuring circuit is the role of Auto Temperature Sensor output power becomes final follow-up show , analytical instruments generally acceptable voltage signal . Therefore, the vibration sensor according to their function may have the following classification : according to the principle of mechanical Receive : Relative type, inertial ; according to the principle of electromechanical conversion : electric , piezoelectric , eddy current , inductive , capacitive, resistive, photoelectric ; measured by the amount of machinery : displacement sensor, speed sensor
Photoelectric sensor is used to detect the distance of the apparatus from the light source is a
Photoelectric sensor is used to detect the distance of the device , a by a light source, an optical path and the three kinds of photovoltaic element part , the following is a detailed description of the photoelectric sensor . A self-contained photoelectric sensors include optical and electronic products , you only need a power supply. The Cooling Temp Sensorsperforms its own modulation, demodulation, amplification, and output switch . Some independent sensors provide such options as built-in control timer or counter. As technology advances, independent photoelectric Crankshaft Positioning Sensor getting smaller. Remote photoelectric sensors for remote sensing or in hard to reach places, contains only one Coolant Temperature Sensor optical components. Power input circuit , amplified, and output switch is in a different location , usually in a control panel . This allows the sensor is very small , and controls are accessible , because they could be bigger. When space is limited or even hostile environment is too remote sensors, optical fiber may be used. Fiber is a passive mechanical sensing components. They can use two remote or separate sensors . They no electrical wiring and no moving parts, can be safely tube light harsh environments.
2013年10月13日星期日
Rocket technology sensor applications
Rocket launch is like a dragon is never caught not come, in fact, on the rocket in order to ensure safe flight of astronauts to provide accurate input data , the rocket on the various types of sensors , converters play an important role in sensor in the end what kind of role play it , and today China sensors trading network came to tell you about it. Various types of Camshaft Position Sensor on the rocket , mostly installed inside the key parts of the rocket , they perceived the arrow on the physical changes responsible for the physical quantity conversion converter to achieve the transmission signal supplied to the control system of the rocket and ground control center as a basis to judge , like a change in both eyes fixed targets for the command center to provide a basis to predict . Speaking of rockets internal sensor , manifold variety. Working principle of a capacitive , resistive , optical type , indicators measured pressure, displacement , strain, physical monitoring the acceleration , position, temperature , noise, vibration , etc. aspects. Wide range of sensors in the rocket world, there are several categories is particularly important, it is a direct monitoring data reflect the status of the rocket is safe . Acceleration sensor lifesaving escape criterion for the rocket escape system provides important parameters , when the rocket a serious failure , endangering the safety of astronauts , it will show the acceleration deviation from the design value , the sensor will sense this change the first time , and issued signal initiates escape procedures to help astronauts quickly out of the woods . Using the system with level Crankshaft Positioning Sensor for measuring the remaining amount of propellant level measurement , real time, continuously , accurately provide information on the remaining amount of liquid propellant , controls the engine adjusting valve or open or closed , monitoring the flow of propellant mixing ratio of the engine keep tank oxidant , the mass ratio of the combustion agent is within the optimal range . Vibration and noise is the rocket invisible killer , though does not seem to explode so violently cruel, but the astronauts of the body is also very large destructive . In order to ensure the rocket during flight vibration and noise generated by the human body can not exceed acceptable levels , improve ride comfort of astronauts , rockets also set up a special monitoring vibration and noise of Car Temperature Sensor. Rumbling avalanche of orange flame , daring and took away all eyes , a small Car Sensors on the huge rocket body seem insignificant , but they are protecting the safety of the astronauts unsung heroes in the thousands of degrees of broiled high stick to their posts , so vacated became an astronaut flying dragon tame car.
Piezoelectric ceramic ultrasonic sensor working principle and structural characteristics
Ultrasonic sensors are developed from the use of ultrasonic sensor characteristics , because of its reliable, easy to install, waterproof , launch angle is small, high sensitivity , are widely used in liquid level monitoring, robot collision avoidance , a variety of ultrasonic proximity switches, and burglar alarm and other related fields. As we all know , is the production of piezoelectric ceramic ultrasonic sensor probes commonly used materials . Here's a look at piezoelectric ceramic Automotive Temperature Sensors working principle and structural characteristics . When a voltage is applied to the piezoelectric ceramics , piezoelectric ceramics will change with voltage and frequency mechanical deformation . On the other hand , when the vibration of piezoelectric ceramics , an electrical charge is generated . Using this principle , when given by the two piezoelectric ceramic or a piezoelectric ceramic and a metal sheet having a vibrator, the bimorph element , applying an electrical signal , it will emit an ultrasonic vibration by bending . In contrast, when applied to the bimorph element ultrasonic vibration , it will generate an electrical signal. Because of these effects , it can be used as a piezoelectric ceramic ultrasonic sensor . The Car Temperature Sensor is a composite vibrator be flexibly fixed on the base . The compound of the resonator and the vibrator consists of a metal plate and a piezoelectric ceramic bimorph element consisting of a combination of the vibrator . Resonator flared aims to effectively radiate ultrasonic waves generated due to vibration , and the ultrasonic waves can be effectively central portion of the vibrator . Piezoelectric ceramic Cooling Temperature Sensor uses a point to note is that in the high- frequency probe , you must use the vertical thickness vibration mode piezoelectric ceramic . In this case , the acoustic impedance of piezoelectric ceramic matches with the air becomes very important . Because the acoustic impedance of the piezoelectric ceramic 105 acoustic impedance of air , which will cause the vibration of the piezoelectric ceramic significant loss of radiation on the surface , then you will need to adhere to a special material on the piezoelectric ceramic ultrasonic sensor , as acoustic matching layer , the air can be realized with acoustic impedance matched , so as to achieve the purpose of the measurement .
Capacitive Humidity Sensor
Capacitive humidity sensor directly sensing the relative humidity changes , the humidity changes into a change in capacitance , and then change in capacitance by the signal conditioning circuit is converted to a standard electrical signal supplied to the associated control or monitoring circuits. Capacitive humidity sensor features are: fast response, high linearity , low hysteresis and long-term stability and good , so applications are increasingly widespread . Capacitive relative humidity sensor usually consists of thermosetting polymers , three capacitor structure , platinum electrodes , as well as integrated signal conditioning circuit ( except for high-temperature applications ) and other components. As shown below, wherein the thermosetting polymer is the outermost layer of the sensor package is mainly for protection against dirt , dust, oil and other Mian override or enter into Camshaft Position Sensor , corrosion platinum electrode , affect the sensor response speed . The outer layer of the platinum electrode is filled with holes, make sure the air with water vapor quickly and smoothly into the internal sensor , speed sensor response speed and reduce the measured hysteresis. In practice , based on the affinity of vapor capacitive, resistive or conductive thin film as a humidity sensor is sensitive to humidity , but also on the temperature-sensitive , so in order to achieve accurate measurement , or wide temperature range , temperature compensation is not necessary small. To achieve temperature compensation, temperature measurements must be placed as close to the Shaft Position Sensor measurement environment, particularly humidity and temperature is calculated using the dew point , which is particularly important. Industrial humidity and dew point measuring apparatus is usually integrated in the sensor substrate opposite a 1000 ohm platinum RTD temperature sensor for temperature compensation. When the sensor sensing area surface temperature is below ambient dew point temperature , then the sensor sensing area surface condensation is easy , even if the surface temperature or sensor sensing area within the local temperature only briefly below ambient dew point temperature, the sensor has an internal or surface condensation may form , especially when the working environment humidity above 95 %, the temperature of the subtle fluctuations are likely to cause condensation . In order to avoid humidity and dew condensation on Crankshaft Positioning Sensor influence , there is usually some measures such as maintaining good air circulation to reduce temperature fluctuations ; add to the humidity sensor sintered stainless steel filter , a waterproof coating to further suppress the condensation of .
2013年10月11日星期五
Note that the actual operation point of the pressure sensor
Measured not only in the production of pressure sensors play an important role , also in real life pressure sensor applications are endless . Pressure sensors are widely automated measurement applications in the automotive market, the new changes almost every day , in fact, everywhere around us , on the road on a motorcycle has a pressure sensor shadow. In fact, the quality of the pressure sensor has been in production concern, in this regard only determines the production and testing department executive power, in fact, the real life of the sensor quality and the right to decide on the user's hand. Here it should be noted that the use of pressure Car Temperature Sensor to make a summary of some of the issues . Pressure sensors work environment is generally more complicated, first of all we should prevent the waste deposited in the conduit and sensors with corrosive or hot media contacts . Measuring gas pressure in the pressure sensor , the pressure port should be opened in the flow line to the top , and the sensor is installed in the flow line to be fixed to the upper part so as to accumulate liquid flow easily into the pipe. Pressure sensors measure the fluid pressure , the pressure port should be opened in the side of the pipeline process , in order to avoid deposition of slag accumulation , this is to prevent blockage causes pressure sensor measurement errors . Impulse control pressure sensor should be installed in temperature fluctuations small place , so as to make the sensor work more stable. Similarly in the measurement of fluid pressure sensor , the sensor should be installed to avoid the impact of the liquid in order to avoid overvoltage damage Cooling Temperature Sensor . Winter freezing occurs when the sensor is installed outdoors freezing measures must be taken to avoid the impulse in the mouth due to icing fluid volume expansion , resulting in loss of the sensor . Pressure sensor wiring , should the cable through the waterproof connector or entangling pipe and tighten the nut tight seal to prevent leakage of rainwater into the transmitter through the cable housing to avoid line fault. Pressure sensor in the measurement of steam or other high temperature medium , the need to take additional buffer tube condenser, the operating temperature of the sensor should not exceed the limit , etc. These problems are in practice the need for technical staff are to pay special attention .
Thin-film temperature sensor is a new type of temperature sensor
Film temperature sensor is a new type of temperature sensor , working principle and common thermal resistance, thermocouple the same , but it's hot junction thickness of only a few microns . Film temperature sensor because of its small , short response time , high sensitivity, ease of integration , etc., suitable for measuring rapid changes in body temperature over time . Film thermocouple principle was first used by the Germans during the First World War made P.Hackmann and developed a film thickness of only 2um thermocouple sensor for measuring bore bullet shot in the foot after a temperature change . Many scholars from around the world followed the film temperatureCamshaftPositioSensorstructure , method of preparation , performance and prospects a lot of research work , and has made encouraging progress in recent years, is widely used in internal combustion piston top surface of the combustion chamber wall and cutting tips and other transient temperature tests . Domestic Northwestern Polytechnical University, Li Fu-Guo Huang Lu , who developed a new right to film thermocouple temperature sensor for measuring the work surface and the internal die temperature transients ; Xi'an Highway University, developed a money orchids, wall heat transfer for internal combustion engines process analysis of the film Coolant Temperature Sensor; Dalian University of Technology precision & processing , Ministry of Education key Laboratory of Bao yuan et al study and produce for measuring cutting temperature NiCr / NiSi film thermocouples.Developed film temperature sensor is the key to solve the coating resistant , solid , impact and insulating layer between the issues and the difficulty of combining domestic and foreign scholars have done a lot of research on the coating process and produce the corresponding thin film sensors. So far, the researchers have developed a thin-film Engine Water Temperature Sensorcan be well applied in some situations , but its versatility deficiencies , and the cost is high ; simultaneously by technology and material constraints , sensor life are generally more shorter.
Acceleration sensor for detecting inclination compensation
Attitude Control System acceleration sensor and tilt sensor can be said that the interaction , the current tilt sensing applications in gesture recognition interfaces will have great potential. Like, in the construction or industrial inspection equipment and other applications, perhaps people are more inclined to one-hand operation . The other hand do not operate the equipment can be freed or operator controlled barrels standing platform , or for security reasons, to seize the ropes. The operator can simply rotate the probe or device to adjust its settings. Like the above case, the triaxial acceleration Shaft Position Sensor senses the inclination can be like that senses a " rotation ": In the presence of gravity tilt speed measured in a state change is detected changes in the gravity vector , and determining a clockwise direction or counterclockwise . These data clearly not a tilt sensor can detect out, tilt detection can also be used in conjunction with one click recognition , so that the operator can control the device with one hand more. Tilt compensation device location measurement Another major application areas in the GPS or the mobile phone of the electronic compass , for example, there is a well-known problem is that when the compass is not placed parallel to the Earth's surface , it will get an error point , in that kind of application, must calculate a bucket with something inclination relative to the Earth in order to accurately draw weight . Pressure is also subject to the influence of gravity , these sensors contain an offset varies depending on the installation position of Crankshaft Positioning Sensor diaphragm . In all these cases , MEMS accelerometer sensing tilt perform necessary , for error compensation . Perhaps the acceleration sensor and the tilt sensor The combination of more use and control, but due to the acceleration sensor , small size, high performance, acceleration sensor market is still equivalent to posture control in an advantage , people will say it includes accelerometer tilt sensor , and inclination angle Crankcase Position Sensor is the master key to measuring the acceleration sensor can be said tilt sensor creative products.
On the role of the acceleration sensor compensation
The most common application acceleration sensor is used to detect the acceleration and direction of the phone , while the phone when it is only by standing gravity , so many people put the acceleration sensor function is also called gravity sensing capabilities. Acceleration sensor 's strengths lie in the force measuring device . Yeah, but the device used to measure the position relative to the ground placed , then the accuracy is not high. Acceleration sensors can be used with a fixed reference coordinate system gravity , there is a linear or rotary motion tilting movement is limited , but a range of applications . Handle both linear and rotational movement , you need to put the acceleration sensor and a gyro sensor combination. If you want the device will not get lost in the movement direction, coupled with Crankshaft Positioning Sensor , a gyro , a magnetic sensor and an acceleration sensor is often used in conjunction with each other there is a mutual compensation between . Application of the magnetic sensor by measuring the magnetic flux electronic compass to determine the size direction . When the magnetic Coolant Temperature Sensor is tilted, the geomagnetic flux through the magnetic sensor will change , so that the direction of the point of error . Therefore, if tilt correction without electronic compass , requiring users to horizontally. The acceleration sensor can measure the angle of this principle, the tilt can be compensated electronic compass . In addition , GPS systems are three by 120 degrees by receiving satellite signals distribution finalize the object orientation . In some special occasions and landforms, such as tunnel, skyscrapers, jungles , GPS signals may be weak or even completely lost , which is called the dead . And through the installation of an acceleration sensor and a common inertial Cooling Temperature Sensor , the system can measure the dead zone . Time integral of the acceleration sensor , it becomes a change in speed per unit time , thereby measure the movement of the object in the dead zone . .
2013年10月9日星期三
Temperature and humidity sensor applications in environmental monitoring
Metro 's large volume, which is a large passenger flow , the required variation in fresh air . Therefore subway air conditioning load changes, to achieve energy must resort to automatic control means. Automatic control system as an integral part of , environmental sensors in the subway more plays an important role . The environmental control system in the subway , the main use of the indoor temperature sensor and humidity sensor , duct temperature and humidity sensors . We can order at the station concourse and platform areas and other public areas as well as important equipment room set indoor temperature and humidity sensors to monitor real-time temperature and humidity of the station . These parameters can help operational staff working conditions of various systems of the station to make reasonable adjustments to keep always in the public areas of the station more comfortable environment to ensure that the device has been in the right room temperature under . Indoor temperature and humidity Car Sensors are generally mounted on the station concourse , platform and equipment room on the wall or on top . In the meantime, we can at the station 's new air chamber and the return air duct temperature and humidity chamber mounted Engine Water Temperature Sensor to monitor the outdoor air and the temperature and humidity inside the station . Environmental control system according to the data collected by sensors to determine the environmental quality of the station , and according to a variety of conditions pre-designed for automatic switch , automatic control system in order to achieve automatic control of the environment of the station , so that the station is always in a more environment comfortable environment, and ultimately achieve the purpose of energy saving and emission reduction . Pipeline temperature and humidity Coolant Temperature Sensor is usually installed in the new and the return air plenum chamber walls. Thus, the temperature and humidity sensor usefulness in life more and more, it is not only in the station , greenhouse , file management and food industry has applied , is now in the subway environmental control system has also been adopted .
Piezoelectric sensors are used in the acceleration pressure and force measurements , etc.
Piezoelectric sensors are used in the acceleration, pressure , and the measurement of force, etc. . Piezoelectric acceleration sensor is a common accelerometer. It has a simple structure , small size , light weight, long life and other excellent features. Piezoelectric Accelerometer in aircraft, automobiles, ships, bridges and construction of vibration and shock measurements has been widely used, especially in the field of aviation and aerospace more of its special status. Piezoelectric Coolant Temperature Sensor can also be used to measure the pressure of internal combustion engine is measured with the measurement of the degree of vacuum . Can also be used in military industry, for example, use it to measure the firing guns and bullets in the chamber in the moment of the change and muzzle bore pressure shock wave pressure . It can be used to measure a large pressure can also be used to measure small pressure . Piezoelectric sensors are also widely used in biomedical measurements , such as the decline of ventricular catheter damper is made of a piezoelectric transducer , as measured dynamic pressure is so common , so the piezoelectric Car Temperature Sensor applications is very broad. In addition to piezoelectric sensors , there are manufactured using the piezoresistive effect of piezoresistive sensors, the use of the strain sensor strain effect , these various pressure sensors using different materials and different effects on different occasions to play them unique purpose.
Capacitive Accelerometer
Capacitance -type ( with changes in acceleration caused by the change in capacitance sensing mass ) acceleration sensor is the most common in today . Irreplaceable in certain areas , such as airbags , cell phones and other mobile devices . High yield and low cost makes such sensors . However, this low signal to noise ratio of the sensor is subject to a low , limited dynamic range . All capacitors type Coolant Temperature Sensor has an internal clock that (~ 500kHz) is an essential part of the detection circuit , the output signal due to leakage often be disturbed. The frequency of this noise is far higher than the measured signal frequency , generally will not affect the measurement result , but it is always and test signals superimposed . A built-in amplifier chip, which generally has a 3-wire ( or 4-wire differential output ) interface. DC power supply will be able to work as long as there is . Capacitance type acceleration Coolant Temperature Sensor working bandwidth is generally limited to a few hundred Hz, partly because of its internal structure with a large and heavy air damping . Capacitance type acceleration sensor suitable for measuring low-range acceleration , the upper limit is generally less than 100g . In addition to these limitations, modern capacitance type acceleration Crank Shaft Position Sensor , in particular a level meter of the device, with good linearity and high stability. Capacitive acceleration sensor is usually appropriate onboard test , low cost is a factor. For low-frequency exercise test , acceleration generally low , they are an ideal choice. Such as civil engineering vibration testing .
2013年10月7日星期一
Precautions for replacement load cell
When replacing the load cell is also requiring attention , correct replacement approach allows the sensor is more convenient to install , click Yes precautions. A weighing sensor increases as the rated load , the output of the micro- volts / division signals are reduced , rather than as the load increases, the output signal also increases . This point is often overlooked . So replacing the sensor should be used as much as possible like the original load sensors. To replace the load slightly larger , we should pay attention to electronic scales weighing indicator range is adjustable : If it is not adjustable old display instruments, because the load into a larger sensor, the output of the micro volts / division signal is smaller, not full-scale output, display , DIP adjust achieving its purpose and can not use ; if it is adjustable range weighing indicator ( such as Toledo 8140 series ) , and replaced with a larger Cooling Temperature Sensor payload after the by setting the range, according to the instructions debugging. Also note that , if the load sensor is too large , the output of the micro -volt / div signal is too small , easy to reduce the sensitivity of the scale . (2) For the second force transmission link ( ie, the first lever and the second force transmission power transmission link between the lever ) S-shaped Crankshaft Positioning Sensor installed in electromechanical integration scale , should pay attention to : Reinstall the sensor after linking rod length with the same length as the original link . On the other hand , is to ensure that the first level of leverage and power transmission link with the first force transmission lever vertical angle of 90 degrees . If there are deviations , the scale will directly affect the accuracy and sensitivity. Link length is too long , a " large scale " phenomenon ; too short , a " small scale " phenomenon . At this point should also note that the link must be in free suspension state , in conjunction with other objects of friction to avoid affecting the sensitivity of the scale . 3 electromechanical integration scale in replacement of Car Sensors debugging, debugging mechanical scales should be based on accurate weighing indicator according to instructions . 4 . Whether electronic or electromechanical integration scale scales , in replacement of the sensor , it must pass through the test before use.
订阅:
博文 (Atom)