Camshaft position sensor, also known as the cylinder identification sensor, camshaft position sensors are generally expressed by CIS. Camshaft position sensor function is to collect the valve camshaft position signal, and input ECU, in order to identify the ECU compression TDC cylinder 1, thereby performing sequential fuel injection control, ignition timing control and knock control.
Cooling Temperature Sensor
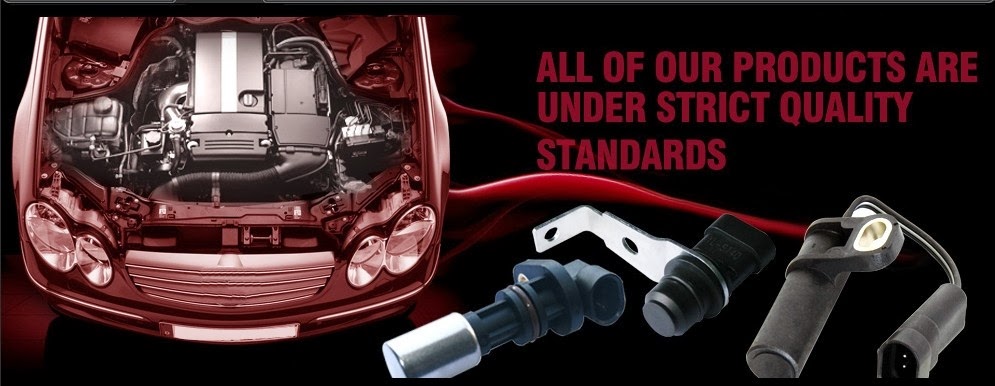
Cooling Temperature Sensor
2013年9月29日星期日
A compound of the ultrasonic sensor is flexibly vibrators fixed to the base
The ultrasonic sensor is a composite vibrator be flexibly fixed on the base . The compound of the resonator and the vibrator consists of a metal plate and a piezoelectric ceramic bimorph element consisting of a combination of the vibrator . Resonator flared aims to effectively radiate ultrasonic waves generated due to vibration , and the ultrasonic waves can be effectively central portion of the vibrator .Piezoelectric ceramic ultrasonic Camshaft Position Sensor uses a point to note is that in the high- frequency probe , you must use the vertical thickness vibration mode piezoelectric ceramic . In this case , the acoustic impedance of piezoelectric ceramic matches with the air becomes very important . Because the acoustic impedance of the piezoelectric ceramic 105 acoustic impedance of air , which will cause the vibration of the piezoelectric ceramic significant loss of radiation on the surface , then you will need to adhere to a special material on the piezoelectric ceramic ultrasonic Automotive Temperature Sensors , as acoustic matching layer , the air can be realized with acoustic impedance matched , so as to achieve the purpose of the measurement .
Ultrasonic sensors are developed from the use of ultrasonic sensor characteristics
Ultrasonic sensors are developed from the use of ultrasonic sensor characteristics , because of its reliable, easy to install, waterproof , launch angle is small, high sensitivity , are widely used in liquid level monitoring, robot collision avoidance , a variety of ultrasonic proximity switches, and burglar alarm and other related fields. As we all know , is the production of piezoelectric ceramic ultrasonic Cooling Temperature Sensor probes commonly used materials . Here's a look at piezoelectric ceramic ultrasonic Car Sensorsworking principle and structural characteristics .When a voltage is applied to the piezoelectric ceramics , piezoelectric ceramics will change with voltage and frequency mechanical deformation . On the other hand , when the vibration of piezoelectric ceramics , an electrical charge is generated . Using this principle , when given by the two piezoelectric ceramic or a piezoelectric ceramic and a metal sheet having a vibrator, the bimorph element , applying an electrical signal , it will emit an ultrasonic vibration by bending . In contrast, when applied to the bimorph element ultrasonic vibration , it will generate an electrical signal. Because of these effects , it can be used as a piezoelectric ceramic ultrasonic sensor .
How to choose a tension sensor housing material
We all know that there are a lot of tension in the sensor characteristics, although a variety of tension sensor measuring principle the same but the application environment is different , in fact, there is also a tension sensor housing a variety of materials , generally used in metal material, the material can be used most of the aluminum alloy , alloy steel materials and stainless steel.Aluminum alloy tension sensor selection is not a lot , this can reduce costs, but the quality will be relatively light . Are generally small scale will choose aluminum alloy, or a requirement to install will choose this material . Stainless steel and aluminum alloy tension Cooling Temperature Sensor is just the opposite , stainless steel is generally used for a large range of force sensor, the sensor so as to ensure no distortion when driving is not damaged. The general quality of the material Shaft Position Sensor is relatively large , the price is also more expensive in general a large range and some high requirements on the use of this material , alloy steel tension sensor is the most common kind of material . In view of this material between aluminum alloy and stainless steel , alloy steel tension sensor can fit most situations apply . Most are available in the market Engine Water Temperature Sensor alloy . Alloy both stiffness and deformation recovery to ensure consistent deformation , corrosion resistance and good weatherability .We choose the force sensor , when in fact it is not too concerned about the material , because the manufacturers in the production time will take into account what kind of material selection , not large range also selected aluminum alloy tension sensor , unless customers have special requirements , the particular bad environment must choose a material of the sensor. Manufacturers generally also be customized according to customer requirements .
2013年9月28日星期六
Contact temperature sensor
As part of this sensor detects between the measured object with a good contact, so again it is usually called a thermometer. It is by conduction or convection and thermal equilibrium state , it can be directly displayed value represents the case of the measured temperature of the object . Generally, it 's measurement accuracy is relatively high . Within a certain temperature , it is even able to measure the temperature inside the object of each case . However, if the measurement is the movement of objects , the heat capacity of small objects or small target, the measurement results will have a relatively large errors , frequent use of the thermometer Engine Temp Sensor thermometer , resistance thermometers , bimetal thermometers and glass liquid thermometers, etc. and so on. They are in the commercial, agricultural and industrial applications are very wide , even in normal life , people often use these thermometers. In electronics, medicine, metallurgy , defense engineering and food sectors , cryogenic technology is widely applied , and there are strong research on superconducting technology , and now you want to measure the temperature of the low temperature below 120K thermometer has been well development , such as : acoustic thermometer, temperature heat thermometer , vapor pressure thermometer, gas thermometer and temperature and so on. Low temperature thermometer element to smaller size , better stability and reproducibility and accuracy is higher. Carburizing heat resistive glass using a porous sintered high-silica glass to form a low temperature carburization thermometer in one temperature sensing element , which can be used to measure 1.6 ~ 300K temperature within this temperature range .
GC-type analyzer
GC-type analyzer is based on chromatographic separation and detection techniques, separation and determination of the concentration of each component in the sample gas, so the whole analytical instruments. In the power plant boiler test, has been applied. Work, periodically from the injector means a volume of gas samples taken in a pure carrier gas flow rate (i.e., the mobile phase) to carry, the flow through the column, the column referred Engine Temperature Sensors stationary phase with a solid or liquid, the use of stationary gas sample, the absorption of the components of the different solubility, the two phases of the components in the distribution is repeated, so that the separation of the components, the column according to time the detector has carried out the quantitative determination. According detection principle, subdivided into concentration detector and mass detector two kinds.
Semiconductor gas sensor
Semiconductor type gas sensor is based on a metal oxide or a metal oxide material made of semiconductor detection element interacts with the gas generated on the surface or reaction, causing movement of carriers characterized by conductivity or volt-ampere characteristics or surface potential changes in the gas concentration measurement. The mechanism from the control surface can be divided into type (using a gas adsorbed on the surface of the semiconductor conductivity changes arising from the sensitive element), surface potential type (adsorbed gas generated after Positioning Sensor of semiconductor surface potential or the zeta potential change of the gas sensitive element), Volume controlled (based semiconductor react with the gas when the volume change, thus changing the working principle of generating electrical conductivity), etc. Percentage can detect concentrations of combustible gases can be detected ppm level toxic and harmful gases. Has a simple structure, high sensitivity, fast response, and many other practical advantages, but its main deficiency is a measure of the linear range is small, by the background gas interferences, susceptible to ambient temperature and so on.
Optical gas sensor
Optical gas sensing technology is a late start, but one of the fastest growing technologies. The type commonly used in industry has an infrared gas analyzer, ultraviolet analyzer, photoelectric colorimeter type analyzer, chemiluminescence analyzer, light scattering analyzerInfrared type working principle is to use infrared absorption spectrum of Engine Temperature Sensors measured gas characteristics or thermal effect to achieve the gas concentration measurement, common spectral range 1 ~ 25μm, the commonly used types of dispersive infrared type DIR and NDIR non-dispersive infrared type. Shimadzu produced SOA-307/307Dx sulfur dioxide continuous analyzers, the measurement method is to use a single light source dual-beam non-dispersive infrared absorption method, namely, by the measured gas broadband infrared radiation with a wavelength selective detector and to select a specific frequency band, in order to this specific wavelength to measure SO2 absorption of infrared radiation, the measurement range of the minimum 0 ~ 100ppm, up to 0 ~ 1vol%.
Magnetic sensor gas analysis
In the magnetic sensor gas analysis, the most common is the use of high magnetic properties of oxygen to measure the oxygen concentration of a magnetic oxygen sensor, measuring the widest range of oxygen, oxygen is a very effective measuring instruments. Commonly used thermal-magnetic convection oxygen analyzer Crank Position Sensors (according to form in different ways, can be subdivided into speed thermal magnetic type, pressure balanced thermal magnetic) and magnetic mechanical analysis of oxygen sensors. Its typical applications are fertilizer production, cryogenic air separation plant, power plant combustion systems, natural gas and other industrial production of acetylene oxygen control and chain, exhaust, exhaust, smoke and other emissions of environmental monitoring.
2013年9月27日星期五
The development of intelligent pressure sensor
With the development of computer and control systems, sensor technology has been further improved, Motor sensor system is now available as an emerging research direction, more and more researchers' attention. His research in recent years, although some results, but for the growing demand is far from satisfying, especially in the pressureShaft PositionSensor product development has become more necessary development. With the pressure measurement and control system development, existing traditional pressure measurement products has been unable to meet the requirements, it usually requires collection of information collection,informationprocessing and digital communication functions in one, to achieve self-management, with intelligent features, so you need to be more intelligentCrank Shaft Position Sensor. Smart sensors are generally with the microprocessor, with the collection, processing, exchange information, Cooling Temperature Sensor integration and microprocessor product of the combination.Usually a feeling of control system in part by a plurality of sensors gathered together, collecting information sent to the computer for processing, after the use of smart sensors can be dispersed in situ processing of information, thereby reducing system cost.
With the demand for consumer electronics, automotive electronics and the expansion of the sensor has also been rapid development
With the demand for consumer electronics, automotive electronics and the expansion of the sensor has also been rapid development. Now, we see a lot of electronic products are often integrated functions, which have a combined sensor inside the credit inside. Expected in the future, the combination of sensor applications will be greater development, sales will gradually soared. Combined sensor is to a variety of Cooling Temperature Sensor products packaged together, so that you can capture a variety of signals, which saves space, but also reduce costs. Now, this applies to Cooling Temperature Sensorand multi-circuit board space is limited or electronic products which, like mobile phones, tablets and so on. The future, six-axis amshaft Position Sensor measurement unit (IMU) will become a mainstream application, play a greater functionality.There is some are mandatory use of specific technology products among applications, the cost become the decisive factor, as the automobile industry, each year in great demand, and if the results too, give car manufacturers to bring great pressure, to save costs, the combination of Car Temperature Sensor is the best choice. Along with that, the development of the automotive industry, the combination of Automotive Temperature Sensors growth momentum will continue soaring addition, the application of the security industry combined sensor. Security industry is now second only to the automotive industry, becoming the second fastest growing areas of the sensor. It is precisely because these areas the expansion of product performance requirements, bringing combined sensor development. With the continuous expansion of the field of future applications, potential business opportunities will be inestimable. As of now, there are many vacancies in combination sensor market, which gives manufacturers also brought a lot of opportunities.
Iron environmental control systems widely used in temperature and humidity sensor
Metro has become an essential transportation in big cities run the tool, it has a large volume, punctuality is good, fast and safe, transport, high efficiency, environmentally friendlyadvantages. As subway passenger trips and more, how to give passengers a comfortable thermal environment satisfactory, becoming the transport sector needs to be considered resolved. This requires careful design of the subway environmental control system in whichtemperature and Engine Water Shaft Position Sensor detection tool is required. Metro's large volume, which is a large passenger flow, the required variation in fresh air. Therefore subway air conditioning load changes, to achieve energy must resort to automatic control means. Automatic control system as an integral part of, environmental sensors in the subway more plays an important role.
2013年9月26日星期四
Railway bridge machine on tilt sensor applications
Tilt sensor is used to specifically measure the tilt angle sensor is able to measure the tilt angle of the object and bridges, inclination Crankshaft Positioning Sensor can real-time monitoring erecting machine tilt angle, and monitor the data transmitted to the control room, monitoring personnel according to the actual situation adjustment of status, to achieve security monitoring. Railway bridge is a machine for railway bridge construction on the common construction machinery, railway bridge machine in the railway tracks on the road, will make the beams onto the bridge piers, and its main function is to beams filed after delivery to a fixed position down. Erecting machine work great mechanical strength, and every time you need to run a large number of objects and even large tonnage, Camshaft Position Sensor to be hanging beams through the bridge embankment on the bit, and take line high center of gravity and axle load, with the massive there may be roadbed and line quality is poor, such as the curved section outer rails high enough to cause the body tilt cause side friction is large, if the friction is more serious and may lead to unnoticed after overturning accident, the line will lead to uneven slope erecting machine slippery, making it appear forward phenomenon, coupled with factors such as human and prone to dangerous accidents to predict in advance, using the tilt sensor is a good solution.
Voltage output accelerometer
Voltage output accelerometer another piezoelectric accelerometer output voltage signal rather than charge signal. This sensor is contained within the charge amplifier. Voltage mode sensor 3-wire (signal, ground, power) and 2-wire (signal / power, ground). 2-wire, also known as IC piezoelectric sensors (IEPE). Because you can easily use coaxial (2-wire, wire and shielded wire) connection, IEPE very popular. In this mode, the AC signal superimposed on the DC power supply. At the output terminal in series with a coupling capacitor to remove the DC bias voltage sensor, so that only access toCooling Temperature Sensorsignal output. Many modern instruments provide IEPE / ICP input interface, which can be directly connected IEPE sensors. If IEPE power supply interface is unavailable, you need a signal amplifier with a constant current source and an IEPE sensor used. 3-wire sensor requires a separate DC power cable supply. With charge output type acceleration sensor is different is that in addition to the piezoelectric ceramic element, the voltage output type acceleration sensor contains a tiny circuit, the circuit limits the operating temperature range of Crankcase Position Sensor's overall operating temperature range, usually no more than 125 ° C. There are also some design increased to 175 ° C, but its other properties will decline. Usable dynamic range - the piezoelectric ceramic element has a very wide dynamic range, charge output type acceleration Motor sensor on the scale is defined is very flexible because of its full-scale charge amplifier can be remotely adjusted freely by the user. The voltage output type acceleration sensor has established a full-scale, which depends on the internal charge amplifier, once produced by the plant will no longer be changed.
The acceleration sensor technology used
AC response acceleration sensors most commonly used AC response acceleration sensor is the use of a piezoelectric element as its sensitive unit. When the acceleration input, the sensor of the sensing mass "move" of the piezoelectric element generates a charge proportional to the input acceleration signal. From the electrical angle of view, as an active piezoelectric element capacitor, its ohmic resistance level at 10x9. Determined by the resistance and capacitance RC time constant, which also determines the frequency of Crankshaft Positioning Sensor through the properties. For this reason, the piezoelectric accelerometer can be used to measure static event. The piezoelectric element may be derived from natural or synthetic. They have different signal conversion efficiency and linearity. There are two types on the market piezoelectric accelerometer - charge output, voltage output. Main charge output piezoelectric acceleration sensor acceleration sensor zirconate titanate ceramics, has a wide operating temperature range, wide dynamic range, wide frequency range (usable frequency> 10kHz). Charge output of the piezoelectric type Camshaft Position Sensor is encapsulated in an airtight ceramic metal housing. Due to the ability to resist harsh environments, which has a very good durability. Because of its high impedance, this sensor requires a charge amplifier and low noise with shielded cable is used, preferably a coaxial cable. Low noise cable is a finger which has a low friction electrical noise, which is generated by the movement of the noise from the cable itself. Many sensor manufacturers also offer this low-noise cable. Charge amplifier and charge output type acceleration Automotive Temperature Sensors connection, which can eliminate the cable capacitance and the impact of the sensor capacitor in parallel. With advanced charge amplifier, charge output type acceleration sensor is easy to achieve wide dynamic response (> 120dB). Since the piezoelectric ceramic is very wide temperature range, some sensors may be used to -200 ° C to +400 ° C, or even wider temperature environment. They are particularly suitable for vibration testing under extreme temperatures, such as turbine engine monitoring.
How the sensor application circuit reduces noise and interference
Sensor circuit sensor circuit noise and interference sources easily received outside or inside some of the irregular noise or interference signals, in fact, passThe success of Crankshaft Sensor Replacement design and interference design are inseparable.Low-frequency noise is low frequency noise is mainly due to internaldiscontinuities caused by the conductive particles. In particular carbon film resistors, the carbonaceous material is present inside many micro-Small particles, particles are discontinuous, the electric current flows through the resistor will change in conductivity caused by the current changes, the contact does not produce similarOrleans arc flash explosion. In addition, the transistor may also have a similar burst noise and flicker noise, and the resistance mechanism which generates a discontinuity in the particle phaseRecently, also the degree of doping of the transistor. Two semiconductor devices produced by the shot noise of the semiconductor PN junction voltage across the barrier zone changes caused tiredThe charge accumulated in this region the number of changes, which show a capacitive effect. When the applied forward voltage rises, N and P areas of electronic devices in the depletion region of the holeMovement, is equivalent to charging the capacitor. When the forward voltage decreases, which in turn make the depletion region away from the electron and hole, the equivalent capacitor is discharged. When the applied reverseVoltage, the depletion region of the opposite variation. When Crankshaft Positioning Sensor flows through the potential barrier region, this change will cause flow through the potential barrier region small fluctuations generated by the current, thereby generatingRaw current noise. Its size and noise temperature, △ f is proportional to the bandwidth. 3 high-frequency thermal noise, thermal noise is due to internal electronic conductorGenerated by the random motion. The higher the temperature, the more intense electron motion. No internal electronic conductor Games in its internal rules the formation of many tinyCurrent fluctuations, because it is disorderly movement, so its average total current is zero, but it as a component (or as part of the circuit) is connected up, A circuit, its internal current will be enlarged to a noise source, especially in the high frequency band of the work circuit of high frequency noise particularly.
How to choose the sensor guide
Sensors can monitor what is very much the scope of application is very extensive , it is also in the choice of the sensor can not be blind choice , requires a certain skill . Select a deciding factor when the sensor is working environments. Some industries ( such as food and automotive industries ) work environment may be dirty or dangerous , or both. In processing food , the humidity may be higher and have a lot of liquid. Processing engine or other parts of the automobile factory workshop, there may be sand , lubricants and coolants . In this case , the sensor must be considered environmental adaptability , if the sensor can not be used not meet environmental dirt . Such considerations also affect the required detection range because Coolant Temperature Sensor may need to be placed in harsh environments outside a distant location ( rather than on the desired location ) . If the light is dirty or signal weakened, then proactively alerting and notification is helpful. Similar environmental problems will affect the sensor size , the size can vary from smaller than a finger into the open palm bigger than that . Large size than the small size of the sensor to the sensor , since all the components are incorporated into a small space, higher cost . Small size of the area to collect light Crankshaft Sensor Replacement is smaller, a detection range of smaller, lower optical performance . To overcome these shortcomings , the small size of the sensor in order to better match the physical space available . Again, in the semiconductor clean room equipment used in the work environment is not bad sensor though , but must work in confined spaces . At a distance of typically a few inches , so Car Temperature Sensor are generally small. These sensors often use fiber to the light import ( or export ) detection zones . Installation and the price is a factor to consider is to install the system . Sensors typically require a box or other means for mechanical protection. This mechanical and optical protection costs may be greater than the cost of the sensor itself is also high, so is the need to consider when buying an important factor . If the firm has a flexible mounting system , as well as protection for the sensor mounting arrangement , the product is easier to achieve and live longer .
2013年9月25日星期三
The pressure sensor of the two methods to achieve impact
Pressure sensors used in many bad environment , some of the bad environment may be more severe , such as pressure Map Sensor need to measure the impact pressure , the measured impact pressure generally requires relatively high pressure sensor performance , we usually have the following two methods to measure the impact type pressure .1, changing the pressure transmitter chip , not an ordinary ceramic cores or diffused silicon core , but with strain gages , strain gauges is a strain on the DUT will be converted into an electrical signal changes in the sensitivity of the device . It is a piezoresistive strain Engine Temp Sensor of the main components .Resistance strain gauge is the most widely used metal resistance strain gauges and semiconductor strain gauges two kinds . Metal resistance strain gauges have filamentous strain gauge and the metal foil strain gages two kinds . The strain gauge is usually via a special adhesive binder tight mechanical strain is generated on the substrate , the force occurs when the substrate stress , the resistance strain gauge is generated with deformation, the resistance strain gauge is changed , so that the the voltage across the resistor changes .The strain gauge force generated when the change in resistance is usually small , it typically are composed of strain gage bridge , and through subsequent instrumentation amplifier is amplified , and then transmitted to the processing circuit . Strain gauge pressure Crankshaft Position Sensor is generally shock and impact resistance is better, but this sensor accuracy with their manufacturers .2 , with ordinary ceramic pressure sensor or pressure sensor to measure diffusion silicon , but not be measured directly , but with the addition of a buffer tube , which also can measure the impact pressure . This method is economical , easy to install , so the application is very extensive.Regardless of the method is to measure the impact pressure sensor core body protection is not strong pressure washed out . Which method based on the specific use now have a bad environment and customer choice .
There are four pressure sensors which strain classification
Strain gauge pressure sensor is a pressure sensor in the application of more of a sensor, usually used to measure the pressure of a large , widely used measurement pipe internal pressure , internal combustion gas pressure, differential pressure and the injection pressure, engine and missile tests in the pulsating pressure, and the various areas of the fluid pressure. Also, the sensor has multiple types, different species have different effects 1 , modular : composition strain pressure sensor, the sensing element can be divided into the elastic member and the elastic strain components feelings . Wherein said Shaft Position Sensor converts the pressure force is transmitted to the elastic strain components strain most sensitive parts , and the strain gauge is attached to the elastic strain components at maximum strain . In fact, the more complex strain and strain tubular beam are of this type .2, the diaphragm : its elasticity sensitive element is clamped circular metal flat diaphragm . The diaphragm is deformed under pressure , the center of the radial and tangential strain of the strain reaches a positive maximum , and the negative edge of the radial strain at the maximum shear strain is zero. So often the two strain gauges were attached to the positive and negative maximum strain point , and then into the adjacent bridge arm bridge circuit to obtain greater sensitivity and temperature compensation.3 , strain beam : measuring small pressure, may have fixed beams or other structural beam intensity . One method is to use the diaphragm pressure transducer Weili dowel passed through to the strain beam, beam fixed at both ends of the maximum strain at both ends and the midpoint of the beam , the strain gauge was attached at these places. There are other forms such a structure , for example, the cantilever can be constituted of the diaphragm or bellows .4 , the tubular strain : Strain tubular barrel known as strain , its elastic sensing element is a thin-walled cylinder closed at one end , the other end with a flange connected to the system under test . Affixed to the tube wall with two or four strain gauges attached to the solid portion half as a temperature compensating plate , the other half as a strain gauge measurement .This Positioning Sensor can also be used convert the measured pressure piston force is transmitted to the strain on the tube or through the diaphragm shape pendant chain transfer measured pressure . Strain tube pressure Cooling Temp Sensor structure is simple, easy to manufacture , applicability, in rockets, artillery shells and dynamic pressure measurement has a broad application .
Photoelectric sensor can be used as the target of laser weapons
For a number of the sensor is very sensitive foods , sensors, and more particularly of the kind can detect almost all of the information, in particular optical sensor can detect visible light, infrared radiation , microwaves, radio signals and other role. Signal output by the sensor is usually sent to other electronic equipment for processing. Sensors and signal processing device contains technology are very important , but also quite complex. With the rapid development of photovoltaic technology , all kinds of photoelectric sensors in a variety of military equipment and weapons system has been increasingly widely used military force against the growing dependence of photoelectric sensors . Photoelectric sensor has a wide range of electronic equipment become an important part of the widely used command , control, communications and intelligence acquisition . Both laser rangefinder , or laser radar , or a variety of laser guidance system , are inseparable from certain types of Shaft Position Sensor . Photoelectric sensors like these weapons fire control system "eyes " and leave them on the radar rangefinder and "see" the laser is reflected back from the target , and thus can not be the target distance and other motion parameters were measured , and the laser-guided missiles or bombs can not be tracked and accurately hit these targets. In general, the goal is tracking a missile " blinding " blinding than turn an ordinary soldier has a higher "efficiency " and therefore , the sensor like the human eye , like a low-energy laser weapons, the main target, even is a low-energy laser weapon 's main target. Moreover , the human eye blinding laser weapons would have been condemned and even banned humanitarian use of laser weapons to attack the sensor is not affected by any reproach . The photoelectric Crank Position Sensor to infrared radiation , or visible light , or both particularly sensitive , and therefore is easier to become a laser target. In addition, the electronic system and the sensor itself is also extremely vulnerable to laser-generated thermal noise and electromagnetic noise interference and can not work properly. Battlefield laser weapons attack photoelectric Positioning Sensor are mainly the following ways : with the appropriate energy laser beam sensor " blinding " , making it impossible to detect or to continue to track the target has been detected . Or, if the sensor is guided weapon to the target , then the blinding will make it lose targets. In summary, since the sensor on the battlefield to play an increasingly important role , but very vulnerable to laser attacks, they have become a prime target for low-energy laser weapons . However, the use of laser weapons to attack the sensor , there are some potential problems, mainly some " killer " mechanism as yet lacking real evidence of success . In addition, by a missile tracking pilots may feel with their own weapon " real " to destroy enemy missiles than adopt a " cheat " approach is just to make it " disoriented " better get psychological satisfaction .
Intelligent pressure sensor indispensable two parts: a pressure sensor core and the computer system.
Intelligent pressure sensor indispensable two parts: a pressure sensor core and the computer system.The pressure sensor, the core is used to measure the effect of pressure parameters measured. Auxiliary sensor for the temperature sensor and the ambient pressure sensor. The role of the temperature sensor is used to detect the primary sensor is working, due to environmental temperature changes or changes in the measured medium temperature pressure-sensitive element to temperature changes according to the temperature correction in order to compensate for temperature changes and the measurement error caused. The role of environmental Crank Position Sensor measure changes in atmospheric pressure work environment in order to fix atmospheric pressure changes on the measurement.Thus, the smart sensor has strong adaptive capacity, it can determine the work environment factors change, make the necessary correction to ensure the accuracy of measurement.Computer hardware system for weak Positioning Sensor output signal amplification, processing, storage, and computer communications. The composition of the system should have the function of its dependent. DTP there is a serial output port to RS-232 data transfer instruction format.Here are just generally introduced smart pressure sensor structure and function, in order to know more details of all the smart pressure sensor can access detailed information or contact with the pressure sensor manufacturers for more intelligent pressure sensors.
2013年9月24日星期二
Thermistor sensor in industrial applications
Thermistor sensor , small size , fast response , high sensitivity , so it is widely used in many fields . Thermistor sensor in industrial applications is very wide, depending on the product model, its scope is also not the same line , specifically the following aspects:A thermistor sensor measurement : As a thermistor temperature measurement sensors are generally relatively simple structure , the price is cheaper . No outside protective layer thermistor can only be applied in a dry place ; sealed thermistor afraid of moisture erosion, can be used in a relatively harsh environment .Since the resistance of the thermistor sensor is large, so the connecting wires and the contact resistance of the resistance can be ignored , so Positioning Sensor at the temperature up to several kilometers of distance measurement applications, multi-use bridge measurement circuit . The principle can also be used as the use of other temperature measurement and control circuit.2 , a thermistor for temperature compensation of Crank Shaft Position Sensor : Thermistor temperature sensor in a certain range to compensate for some of the components humidity . Temperature increases , the resistance increases, causing the temperature errors. And can therefore be of the moving coil circuit will be negative temperature coefficient thermistor manganese copper and then with the resistor in parallel with the series compensation components , in which to offset the error caused by temperature changes .In transistor circuits , logarithmic amplifier, is also commonly used thermistor composition compensation circuit. Compensation due to temperature drift errors .3 , thermistor sensor overheat protection: thermal protection of direct indirect protection to protect profits . The small current case, the thermistor Ect Engine Coolant Temperature Sensorcan directly load string person , to protect the device to prevent overheating damage , for large current applications , can be used for the relay , transistor circuit protection.In either case, the thermal resistance of the device to be protected are close together , so that heat exchange between the full , the event of overheating , the protective effect of the thermistor . For example , the stator winding of the motor thermistor embedded in the mutant and in series with the relay . When the motor is overloaded, the stator current increases , causing fever . When the temperature is higher than point mutations , the current in the circuit can be within a few tens of milliamperes is mutated to tens of milliamps , the relay, in order to achieve thermal protection.4 , the thermal resistance sensor for measuring the liquid level : NTC thermistor sensor is applied to a heating current , its surface temperature will be higher than the ambient air temperature , its resistance is small at this time . When the liquid and higher than its installation height, it would take away the heat of the liquid , so the temperature drops , the resistance increased.Determine its resistance changes , you can know whether the liquid level is below the set value . Oil level in the tank car alarm sensor is produced using the above principle . Thermistor in the car is also used to measure the oil , the cooling water mixed with other .
Silicon miniature pressure sensor applications
Manufactured using micro-machining techniques typical product is a silicon micro- pressure sensors , which are U.S. Japan and Europe, the formation of industry . Silicon has developed rapidly in recent years, miniature pressure sensor , the sensor is mainly used in the automotive industry and healthcare fields.Silicon micro- pressure sensors are characterized by small size , light weight, no moving parts , high reliability , but also large-scale production of Crankshaft Position Sensor , so the cost is low. High reliability and low cost requirements for the automotive industry can be said to be very suitable, so in the automotive industry rapidly expanded its applications.Such as automatic brake system pressure car surface pressure , tire pressure , bladder pressure , transmission fluid pressure , fluid pressure injection system , fuel injection pressure, engine oil pressure . Intake manifold pressure has the amount of silicon micro pressure sensor useless .Silicon micro- pressure Crankshaft Sensor in the field of health care products is the largest application of blood pressure monitor. Allegedly some large medical equipment manufacturer to be used each year nearly 5 million pressure sensors. In addition, if the pressure of women with uterine dystocia time monitoring of silicon micro- pressure sensors, intravenous injection of liquid flow monitoring sensors , etc. are a considerable number of market demand. Many other healthcare applications are being constantly developed.Silicon miniature pressure Crank Angle Sensor is basically divided into two types : capacitive and piezoresistive . Capacitive pressure sensor includes a membrane , which acts as one plate of a variable air capacitor , when the pressure on the film , the film is displaced , thereby changing the capacitance value through the appropriate use of such change processing circuit , the pressure can be obtained values. Silicon piezoresistive pressure sensors will produce a resistance change principle made , generally the four strain resistance silicon material constituting the Wheatstone bridge to measure pressure .
Thanks to electronic scales weighing load cells can
Life, people always say , everyone who wants to lose weight crush , just weigh weight , there will be a determination to lose weight . The weigh is inseparable from electronic scales, electronic scales Why can then weigh this depends on a load cell inside presence .Electronic weighing scales Crankshaft Position Sensor can be said that the most important one of the components , in addition to the load cell and then is IC, mainly for two core components , the load cell itself is only an analog signal , when a weight of pressure to the load cells at when the elastic element in Crankshaft Sensor will produce a deformation about this change in the load change of about 1mm .When deformed , attached to the elastic element above minor resistance strain gauges will be pulled up and bent wire cut , totaling four resistors, in accordance with the principle of a Wheatstone bridge , when the resistance strain gauge will move up and bending resistance to two a change in direction , a negative direction is a positive direction , the value is read by our this difference , the amount of difference between the different type of deformation , but this is linearly proportional to , of course, there are some small errors.This error is because of the location and materials and other influential patch , we call it non-linear . So when a platform scale factory calibration and calibration we all need , from two considerations, one is the output , one is non-linear .This is the original strain gauge output , this output signal is very weak , thenormal situation , so take this signal processing IC , so that users can read people understand Kg and pound figure.
How the sensor application circuit reduces noise and interference
Sensor circuit sensor circuit noise and interference sources easily received outside or inside some of the irregular noise or interference signal , in fact, the success Engine Water Temperature Sensor design and interference design are inseparable.A low-frequency noiseLow-frequency noise is mainly due to internal discontinuities caused by the conductive particles . In particular carbon film resistors, the carbonaceous material is present inside many small particles , particles are not continuous, the current flows through the resistor will change in conductivity caused by the current changes, resulting in poor contact of a similar arc flash explosion . In addition , the transistor may also have a similar burst noise and flicker noise , and the resistance mechanism which generates discontinuity of particles similar to , but also the degree of doping of the transistor .2 semiconductor device generates shot noisBecause the semiconductor PN junction voltage Crank Shaft Sensor the potential barrier region caused by changes in the cumulative amount of charge in this region changes, which show a capacitive effect . When the applied forward voltage rises , N and P areas of electronic devices in the depletion region of the hole movement , is equivalent to charging the capacitor . When the forward voltage decreases , which in turn make the depletion region away from the electron and hole , the equivalent capacitor is discharged. When the applied reverse voltage, the depletion region opposite variation . When the current flows through the potential barrier region , this change will cause flow through the potential barrier region small fluctuations generated by the current , thereby generating current noise. Its size and noise temperature , △ f is proportional to the bandwidth .3 high-frequency thermal noiseHigh-frequency thermal noise is due to the internal conductor random motion of electrons generated . The higher the temperature , the more intense electron motion . No internal electronic conductor Games in its internal rules the formation of many small current fluctuations , because it is disorderly movement , so its average total current is zero , but it as a component ( or as part of the circuit ) is connected enlarge circuit , its internal current source will be enlarged to a noise , especially in the high frequency band of the work circuit of high frequency noise particularly .
2013年9月23日星期一
Modular throttle position sensor
Modular throttle position sensor(A) structural features modular TPS Toyota car uses modular throttle position sensor as shown in Figure 2-35a, the principle of the circuit shown in Figure 2-35b. It mainly consists of a variable resistor and the sliding contacts, throttle shaft, idle contact, shell composition. Variable resistor film resistor formed on Crankshaft Sensor board, the variable resistor wiper rotates together with the throttle shaft, sliding arm connected to the output terminal VTA. (2) Combined Combined TPS TPS output characteristics of the output characteristics shown in Figure 2-36. When the throttle is closed or opening is less than 1.2. When the idle contact is closed, its output terminal IDL output low (0V); when the throttle opening is greater than 1.2. When the idle contact is disconnected, the output terminal IDL output high (5V). When the throttle opening change, the variable resistor wiper will immediately rotate the throttle shaft, will be in sliding contact arm slides on film resistor, the Position Sensor output terminal VTA and E, the signal voltage between the ensuing change, as shown in Figure 2-35, the greater the throttle opening degree, the higher output voltage. The linear sensor output signal after A / D converter into a digital signal and then enter the ECU.
Contact switch type throttle position sensor
Contact switch type throttle position sensor( A ) structural features contact switch type TPS Throttle Position Sensor type contact switch (TPS) mainly by the throttle shaft , heavy duty contacts [ also known as power contacts (PSW)], cams, idle contact (IDL ) and wiring socket components. The cam follower throttle shaft , the throttle shaft with the rotation of the throttle opening degree size .
2 ) contact switch type TPS output characteristics of the contact switch type throttle position sensor output characteristic shown in Figure 2-34 . When the throttle is closed , idle contact is closed , the power contacts (PSW) is disconnected, idle contact output terminal of the signal is low , " 0" , the power contacts (PSW) output terminal of the signal is high Ping "l". ECU receives two input signals TPS , if the vehicle speed Motor Sensors input signal indicates the ECU speed is zero , then the ECU determines the engine is idling and increased fuel injector fuel injection quantity control to ensure stable engine idle speed without stalling . If at this time the ECU speed sensor input signal indicates the speed is not zero , then the ECU determines the engine is decelerating state and control fuel injection is stopped to reduce emissions and improve economy . When the throttle opening increases , the cam shaft with the throttle open and the top contact idle , power contacts (PSW) is left open , IDL terminal outputs HIGH "1", PSW pin output is also high level "1 ." Two high-level ECU receives the signal, it is determined that the engine is part of the load state where the ECU based on the crankshaft Auto Temperature Sensor signal and the air flow speed signal calculated and determined amount of fuel injection , the engine main guarantee economy and emissions performance.When nearly all of the throttle opening ( 80% load) , the cam rotation of the power contacts (PSW) is closed , PSW terminal outputs low level "0", IDL kept open and the output terminals of the high level "1 ." ECU receives the two signals, it is determined that the engine running at high load condition , thereby controlling the fuel injector to increase fuel injection quantity, to ensure sufficient engine output power , it will be called the power contacts contact a large load .
When full throttle , ECU will control the system into open-loop control mode, then do not use the oxygen Positioning Sensor signal. If the car air conditioner is working at this time , then the ECU will interrupt the air conditioner main relay signal for approximately 15s, to cut off the electromagnetic clutch coil current conditioner , the air conditioning compressor is stopped, increasing the engine output power, increase the power of the car .
2 ) contact switch type TPS output characteristics of the contact switch type throttle position sensor output characteristic shown in Figure 2-34 . When the throttle is closed , idle contact is closed , the power contacts (PSW) is disconnected, idle contact output terminal of the signal is low , " 0" , the power contacts (PSW) output terminal of the signal is high Ping "l". ECU receives two input signals TPS , if the vehicle speed Motor Sensors input signal indicates the ECU speed is zero , then the ECU determines the engine is idling and increased fuel injector fuel injection quantity control to ensure stable engine idle speed without stalling . If at this time the ECU speed sensor input signal indicates the speed is not zero , then the ECU determines the engine is decelerating state and control fuel injection is stopped to reduce emissions and improve economy . When the throttle opening increases , the cam shaft with the throttle open and the top contact idle , power contacts (PSW) is left open , IDL terminal outputs HIGH "1", PSW pin output is also high level "1 ." Two high-level ECU receives the signal, it is determined that the engine is part of the load state where the ECU based on the crankshaft Auto Temperature Sensor signal and the air flow speed signal calculated and determined amount of fuel injection , the engine main guarantee economy and emissions performance.When nearly all of the throttle opening ( 80% load) , the cam rotation of the power contacts (PSW) is closed , PSW terminal outputs low level "0", IDL kept open and the output terminals of the high level "1 ." ECU receives the two signals, it is determined that the engine running at high load condition , thereby controlling the fuel injector to increase fuel injection quantity, to ensure sufficient engine output power , it will be called the power contacts contact a large load .
When full throttle , ECU will control the system into open-loop control mode, then do not use the oxygen Positioning Sensor signal. If the car air conditioner is working at this time , then the ECU will interrupt the air conditioner main relay signal for approximately 15s, to cut off the electromagnetic clutch coil current conditioner , the air conditioning compressor is stopped, increasing the engine output power, increase the power of the car .
Bimetal temperature sensor cold start timer switch works
When the engine is cold state, the timer switch contacts are closed. When a cold start, the ignition switch is in the start position, the starter power supply terminal, a current flows. Current from the battery through the ignition switch, cold start injector, timer switch bimetal, contacts, ground to form a loop, so that the cold start injector nozzle. At the same time, but also a current flowing through the timer switches the heating coil, two heating coils to heat the bimetal, which is bent when Crankshaft Sensor Replacement contacts, the cold start injector to stop fuel injectionAfter starting, the starter switch is turned off, the ignition switch from the starting position to the open position, no current flows through the cold start injector, to stop fuel injection. Meanwhile, the two heating coils are turned off, but this time the engine is in a warm state, which temperature rises enough to bend the bimetal, the contacts are open, that is the normal operation of the engine, the cold start injector time switch contacts remain disconnected state, not the cold start injector fuel injection.Car manufacturers are based on its own design requirements of the cold start injector time switch operating temperature, such as Nissan series of 18 ℃ below, Toyota series is below 35 ℃. The lower the temperature, the cold start injector working longer. Injector cold start fuel injection valve opening time depends on the length of time.
Bimetal temperature sensor structure
Bimetallic temperature sensor is the use of a bimetal made of a temperature characteristic of temperature Position Sensor, such as cold start timer switch, which consists of housing, bimetal, heating coils, contacts and the like.
Cold start time switch is a temperature-time switch with threaded connections installed at the outlet of the engine, in order to detect the engine coolant temperature. This switch has a normally closed contact inside its movable arm by a pair of sheet metal. Bimetal thermal expansion coefficient from the two different pieces of metal bonded, as the temperature changes, the two thermal expansion difference between the metal sheet, the temperature is low, the bimetal to maintain the original state; temperature rises to a certain extent when the bimetal to the low thermal expansion coefficient of the metal sheet is bent. Bimetal around which two heating coils, heating the bimetal can bend, so the contacts open. Warm up the engine to a certain temperature, the original closed contact should be disconnected.
Cold start time switch is a temperature-time switch with threaded connections installed at the outlet of the engine, in order to detect the engine coolant temperature. This switch has a normally closed contact inside its movable arm by a pair of sheet metal. Bimetal thermal expansion coefficient from the two different pieces of metal bonded, as the temperature changes, the two thermal expansion difference between the metal sheet, the temperature is low, the bimetal to maintain the original state; temperature rises to a certain extent when the bimetal to the low thermal expansion coefficient of the metal sheet is bent. Bimetal around which two heating coils, heating the bimetal can bend, so the contacts open. Warm up the engine to a certain temperature, the original closed contact should be disconnected.
2013年9月22日星期日
On the pressure sensor and the difference between the pressure switch
Many people can not distinguish between pressure sensors, pressure switch and pressure switches difference, today we highlight some of the pressure sensor, pressure switch and pressure switch what is the difference?The pressure sensor is a pressure-sensitive element and a conversion circuit, the use of the measured medium pressure acting on the pressure-sensitive element to produce a slight change in current or voltage output. Sensors often need to be used in conjunction with an external amplifier circuit is detected from the pressure to complete control, display and other processes. Since the pressure Crank Position Sensors is a primary element, the pressure sensor feedback signal must be processed through the monitoring system, analysis, storage, control, allowing operation of industrial automation equipment and engineering controls, and more intelligent. Pressure relay is the use of fluid pressure to open and close electrical contacts electrohydraulic switching signal conversion element. For the relay when the system pressure reaches the set pressure, the issue of the electrical signal controlling the operation of components, to achieve the loading or unloading pump control to perform the operation of the sequence of components, the security protection and interlocking. It is the pressure - displacement transfer member and the micro-switch of two parts. Pressing force - displacement structure type conversion components of view, there plunger, spring, diaphragm and bellows-type four types. Where the structure of a single piston and dual piston plunger two. And can be divided into single-piston plunger, differential piston and plunger - leverage three types. Press contacts to points of single contact and double electric shock. Pressure switch according to the set size of the pressure reaches the set value, the automatic switching on or off the function. Pressure switch, pressure switch, only in your given pressure, open or close the switch, used for simple position control, all digital outputs! Pressure switch pressure switch can provide more than the output node or nodes type. Pressure Position Sensor output may be an analog signal or may be a digital signal, the post-processing convenience, the transmitter signal can become the standard for remote transmission.
Optional temperature and humidity sensors also attach importance to factors such as cost and maintenance workload
Optional temperature and humidity sensors also attach importance to factors such as cost and maintenance workload:Value for money: selection of temperature and humidity meter, you can not only consider the price is low enough, it should be comprehensive price and performance to choose. This includes the price, life, maintenance, calibration costs. Check: validation methods and to consider whether it is easy to make, even if you do not need high-precision results. For convenient on-site and in-situ calibration of the instrument will save you effort. Rugged: hygrometer Engine Temp Sensor and the housing can withstand condensation to take into account, dry, extreme temperatures, dust, chemicals, or other contamination. Quality and reliability, the average life: the poor quality of the judgment, starting from the overall impression, study quality appraisal and factory standards, study the manufacturer's history, reputation, market share and application, brand-name products better than the average, professional manufacturers product is better Auto Temperature Sensor side of the manufacturers, consulting other users is also a good way. Adaptability: not a single one kind of usage, consider the adaptability of the instrument. Battery Tester | Phase sequence tables | Multimeters | Power Meters | Oscilloscopes | Resistance Tester | Resistance Meter | Meter | Clamp | Gauss meter | Electromagnetic Field Tester Replacement: The general hope hygrometer can be used interchangeably with the probe or other your host. Maintenance: regular cleaning visits hygrometer, update, replace the timing requirements. Alternate sex: spare parts for most users is indispensable to investigate whether the supplier can easily provide timely spare parts required.
Sealing means of the humidity sensor, for the protection of the measurement accuracy and stability
Humidity sensor non-sealing, to protect the measurement accuracy and stability, should be avoided in acidic, alkaline, and an atmosphere containing organic solvents used. Also avoid the use of larger dust environments. Space to be measured as accurately reflect the humidity sensor should be placed to avoid too close or away from the wall of the dead at the air does not circulate. If the measured room is too large, it should place multiple sensors. Some of the humidity sensor on the power supply requirements are relatively high, otherwise it will affect the measurement accuracy. Mutual interference between Camshaft Position Sensor or even not work. Should be used in accordance with the technical requirements to provide appropriate and meet the accuracy requirements of the power supply. Sensors will require long-distance signal transmission, pay attention to the signal attenuation problem. When the transmission distance of more than 200m above, suggested the use of the frequency of the output signal humidity sensor. In addition, there are some selection criteria, the use of different temperature and humidity measuring principle, temperature and humidity meter varied to be considered in the selection of the user's actual application environment and requirements, such as range, output and display, installation, sampling methods, gas type, materials and structures, control monitoring requirements, and other environmental hazards. Positioning Sensor network of experts to provide Honeywell Relative humidity / temperature sensor and relative humidity sensors are used to provide on-chip containing a signal conditioning functions integrated circuits. This series of Motor Sensors installed in the thermosetting resin having a polymerization capacitive sensing diaphragm in vivo, interact with the platinum electrode. The use of laser correction of sensor has strong stability and low drift characteristics, with an accuracy of +5% relative humidity. Best use of the environment: Absorption humidity sensors can provide temperature and% RH (relative humidity) output. On-chip signal processing functions can be guaranteed with a relative humidity corresponding linear voltage output. Sensors Laser amended to an accuracy of + 5% relative humidity, calibration accuracy up to 2% relative humidity. The product packaging can be protective chemicals, operating temperature range is -40 ℃ ~ 85 ℃ (-40 degrees to 185 degrees F), in harsh work environments.
Optional temperature and humidity sensors , note range, the measurement accuracy selection
Optional temperature and humidity sensors need to pay attention to measurement range , measurement accuracy of selection ; while also taking into account the time drift and drift and other key factors. Other, The humidity sensor non- sealing , to protect the measurement accuracy and stability , should be avoided in acidic, alkaline , and an atmosphere containing organic solventsBe used. How to buy See article detailed analysis.1 Select the measurement rangeAnd measuring weight, temperature , the choice of the humidity sensor must first determine the range of measurement. In addition to weather , research departments, to engage in temperature and humidity controlThe generally do not need all wet process (0-100% RH) measurements.2 Select the measurement accuracyAccuracy is the most important indicator of the humidity sensor , each increase - percentage points , it is the humidity sensor to a higher level , or even onA grade. To achieve different accuracy because its manufacturing costs vary widely , the price is also very different. Therefore, the user must be tailored, notShould the blind pursuit of "high, fine, sharp ." As at different temperatures andhumidityCamshaftPositioning Sensor, which shows the value of the temperature drift effects should also be considered . As we all know ,Relative humidity is a function of temperature , temperature of seriously affecting the relative humidity within the specified space . Each change of temperature 0.1 ℃. Will generate 0.5% RH humidityChange ( error). If it is difficult to do using the occasion thermostat , theproposed high measuring precision is inappropriate.In most cases, if there is no precise temperature control means , or a non- sealed space is measured , ± 5% RH of accuracy is sufficient . For applications requiring fineIndeed controlled constanttemperature and humidity of the local space , or need to keep track of changes in humidity recording of the occasion, and then use more than ± 3% RH humidity sensor accuracy. The accuracy better than ± 2% RH sensor calibration requirements but even the standard humidity generator is also difficult to do , not to mention Position Sensor itself . Relative humidityMeasuring instruments , even at 20-25 ℃ under 2% RH to achieve the accuracy is still very difficult. Product information is usually given characteristics at room temperature ( 20℃ ± 10 ℃) and the clean gas measurements .3 Consider when the drift and driftIn actual use, due to dust, oil and of harmful gases , use over time , produce electronic humidity sensor aging, precisionDecline in electronic humidity sensor drift is generally within ± 2% or even higher . Under normal circumstances , the manufacturer would have marked a second calibrationEffective use of time is 1 or 2 years , due for re-calibration.
2013年9月21日星期六
Bimetal temperature sensor
Bimetallic temperature sensor is the use of a bimetal made of a temperature characteristic of Crankshaft Position Sensor, such as cold start timer switch, which consists of housing, bimetal, heating coils, contacts and the like.Cold start time switch is a temperature-time switch with threaded connections installed at the outlet of the engine, in order to detect the engine coolant temperature. This switch has a normally closed contact inside its movable arm by a pair of sheet metal. Bimetal thermal expansion coefficient from the two different pieces of metal bonded, as the temperature changes, the two thermal expansion difference between the metal sheet, the temperature is low, the bimetal to maintain the original state; temperature rises to a certain extent when the bimetal to the low thermal expansion coefficient of the metal sheet is bent. Bimetal around which two heating coils, heating the bimetal can bend, so the contacts open. Warm up the engine to a certain temperature, the original closed contact should be disconnected.
Transistor temperature sensor
Transistor temperature sensor In a constant current, the silicon transistor between the base and emitter of the bias voltage varies with the temperature, according to this principle, is made of the transistor temperature Shaft Position Sensor. For example MTS102 sensor, when the temperature is -40 ~ 150 ℃ range, the accuracy is ± 2 ℃, the temperature coefficient of-2.25mV / ℃. With a plastic housing, the response speed in the air as 8s, placed on the response speed of the liquid and 3s.
Diffusion resistance temperature sensor
Diffusion resistance temperature sensorResistor formed on the silicon semiconductor electrode, a voltage is applied when the electrode, the resulting change in the diffusion resistance with temperature. This feature can be made using a temperature sensor. So that it can get low cost, the excellent performance of the sensor. Resin-based Engine Coolant Temperature Sensor response speed, the air of 5s, the temperature coefficient of 0.72% / ℃, than nickel wire resistance type sensor 0.5% / ℃ 22% higher.
Thermistor temperature sensor ferrite
(1) Structure thermistor temperature Coolant Temp Sensor from the shell ferrite, ferrite, the reed switch and a permanent magnet, and the like. Magnetic reed switch in the circuit configuration of two annular permanent magnets and ferrite. The use of ferrite magnetic properties with drastic temperature changes, so that the reed switch is turned on or off. Such Shaft Position Sensor are generally used to control the electric car radiator fan and hydraulic lights.(2) Work Thermal ferrite is a ferromagnetic material, when more than a certain temperature, the permeability of the ferrite sharply, which has a ferromagnetic body from the paramagnetic (weakly magnetic) rapidly changing nature of such abrupt changes in temperature called the Curie temperature. Curie features you can make use of the reed switch is turned on or off.Need to use different sintering material composition and heat treatment methods available in different Curie temperatures. For example, to control the engine cooling water temperature is maintained at 65 to 100%: between two ferrite when the Curie temperatures of 100 ℃, 65 ℃, the corresponding temperature range of the magnetic field strength becomes the form shown in Figure 2-6 shows the flux ring.When the ambient temperature is lower than the thermal ferrite 65 ℃, the two ferrite ferromagnetic material magnetized by the permanent magnet, and with the formation of a magnet and reed switch the contacts of the magnetic field lines through a through and produce suction, so that contact is closed, as shown in Figure 2-6a. When the ambient temperature is higher than the thermal ferrite 100 ℃, two ferrite permeability sharply, into a normally magnetic material is not substantially sensitive magnetized ferrite, ferrite exists no equivalent . Magnetic field of the permanent magnet, the reed switch contacts and generate a magnetic field lines through the suction, the contact is closed, as shown in Figure 2-6c. When the ambient temperature sensitive ferrite 65 ~ 100 ℃ in between, wherein a Curie temperature of 65 ℃ ferrite magnetic material into a normally is not magnetized, and 100 ℃ becomes ferromagnetic ferrite body which is magnetized and the permanent magnet is formed with the left one magnet. ThenReed switch lines through the contacts and generates a magnetic repulsive force, the contact opens
2013年9月17日星期二
Piezoelectric effect is the main working principle of piezoelectric sensors
Piezoelectric effect is the main working principle of piezoelectric sensors , piezoelectric sensors can not be used for static measurements, because after the charge after the external force , only in the loop has infinite input impedance when preserved. The actual situation is not like this, so this can only be decided piezoelectric sensors measure dynamic stress . Piezoelectric sensors are used in the acceleration, pressure , and the measurement of force, etc. . Piezoelectric acceleration Engine Temperature Sensors is a common accelerometer. It has a simple structure , small size , light weight, long life and other excellent features. Piezoelectric Accelerometer in aircraft, automobiles, ships, bridges and construction of vibration and shock measurements has been widely used, especially in the field of aviation and aerospace more of its special status. Piezoelectric Engine Temp Sensor can also be used to measure the pressure of internal combustion engine is measured with the measurement of the degree of vacuum . Can also be used in military industry, for example, use it to measure the firing guns and bullets in the chamber in the moment of the change and muzzle bore pressure shock wave pressure . It can be used to measure a large pressure can also be used to measure small pressure
Principles and Applications of Piezoelectric pressure sensors
Mainly used in the piezoelectric transducer comprises a piezoelectric material are quartz, potassium sodium tartrate , and ammonium dihydrogen phosphate . Where quartz ( silicon dioxide) is a natural crystal , the piezoelectric effect is found in the crystal , and in a certain temperature range, the piezoelectric properties have been present,Engine Coolant Temperature Sensor temperature exceeds this range , the piezoelectric properties completely disappearance ( this temperature is called the " Curie point" ) . As with slight changes in stress field change ( it said piezoelectric coefficient is relatively low ) , so the quartz piezoelectric crystals gradually being replaced by another . The piezoelectric potassium sodium tartrate has great sensitivity and the piezoelectric coefficients , but it is only at a relatively low temperature and humidity environment, it can be applied . Ammonium dihydrogen phosphate crystals are artificial , can withstand high temperatures and high humidity , so has been widely used. Are also used in the polycrystalline piezoelectric effect , the piezoelectric ceramic such as the present , including barium titanate piezoelectric ceramic , PZT, niobate -based piezoelectric ceramics , lead magnesium niobate piezoelectric ceramic and so on.
The circuit can ensure the strain sensor bridge circuit supply
The circuit can ensure the strain sensor bridge circuit power supply, and the strain bridge imbalance signal is converted to a uniform signal output (0-5,4-20 mA or 0-5V). In absolute pressure Crank Shaft Sensor and transmitter, sapphire sheet, ceramic base with glass solder connected together, played a role in the elastic element, the measured strain gauge pressure transducer is deformed so as to achieve the purpose of the pressure measurement.
Silicon - sapphire semiconductor sensitive element manufacturing pressure sensors and transmitters
Silicon - sapphire semiconductor sensitive element manufacturing pressure sensors and transmitters, can work in the harshest working conditions andhighreliability, good accuracy, the temperature error is extremely small, cost-effective.Gauge pressure Engine Temperature Sensors and transmitters by a double diaphragm components: titanium and titanium alloys measuring diaphragm receiving diaphragm. Heteroepitaxial printed bridge circuit of strain sensitive foil sapphire, titanium is welded to the measuring diaphragm. Measured pressure on the diaphragm to the receiver (receiver between the diaphragm and the measuring diaphragm connected together with sturdy rod). Under the action of pressure, the diaphragm is deformed alloy receiver, the deformation by silicon - sapphire perception sensitive element, its output will change the bridge, the magnitude of change is proportional to the measured pressure.
2013年9月16日星期一
Air conditioning controls
Mixed air valve actuators. Mixing air valve using an electrically controlled actuator motor, according to the temperature set by the driver, the automatic control of the mixing air valve position to control the temperature of a certain vehicle. Some models use a vacuum motor, but the control is not precise enoughAir conditioning circuit When the driver when the set temperature of 22 ℃, while the inside temperature is lower than 22 ℃, the control system sends commands to the motor ECU, mixing air valve evaporator side channel and open the heat sink from the heating side to the channel , the interior temperature rises rapidly to 22 ℃,; when the driver setting temperature of 22 ℃, while the inside temperature is higher than 22 ℃, the control system sends commands to the motor ECU, the mixed air from the evaporator side Shaft Position Sensor valve is opened to channel and close the heating heat sink side of the channel, and to high speed blower motor, the inside temperature decreased rapidly to 22 ℃.Analog valve actuators. Analog electronic electronic valve actuator motor control air valve position, thereby changing the air conditioning vent.Compressor control circuit Air conditioning compressor clutch. When the driver selects the A / C mode, the air conditioning system ECU the compressor clutch coil grounding, contact closure, the current through the coil clutch, the clutch combined with disk drive compressor rotation.Check the compressor clutch When the outside temperature is below the set temperature display returns rescheduling value, ECU work of the compressor clutch; Similarly, when Crankshaft Position Sensorshows the engine at full throttle or high speed, ECU work of the compressor clutch.
Audi A6 air conditioning controls
Mixed air valve actuators. Mixing air valve using an electrically controlled actuator motor, according to the temperature set by the driver, the automatic control of the mixing air valve Cooling Temperature Sensor to control the temperature of a certain vehicle. Some models use a vacuum motor, but the control is not precise enough.
Interior temperature control principle
1, outside temperature thermistor sensor is generally made when the outside temperature changes its resistance to change. Low temperature resistance, high temperature resistance is smallCompressor control principle2, the interior temperature sensor uses the same thermistor material having a negative temperature coefficient. Generally installed under the dashboard and the air tube to the air conditioning and ventilation tube, when the air flow rapidly through, the resulting vacuum the air led through the interior temperature sensorSchematic flow distribution 3, sunlight Engine Coolant Temperature Sensor is made of light diodes, or cells, for sensing the intensity of sunlight vehicle, but not the temperature. Usually mounted on top of the dashboardEvaporator temperature sensor control circuit 4, the evaporator temperature Crank Sensor is usually installed on the evaporator fins, in order to accurately evaporator temperature sensor, manufactured using the same thermistor having a negative temperature coefficient.Automatic air conditioning work5, the implementing agencyBlower speed control. Conditioning system ECU according to the set temperature, the temperature existing inside, outside temperature, sun (quotations image parameters) strength, temperature and other signals evaporating dish, to send different commands to the blower motor, and to the grounding, thereby controlling the different the blower speed. For some temperature conditioning system, when the engine is started or when the coolant temperature is below a predetermined value, the blower air conditioning system ECU does not work.
Automotive automatic air conditioning application temperature sensor works
Automotive automatic air conditioning application temperatureCoolant Temp Sensor worksAutomatic temperature control system types and working principle automotive air conditioning Automatic temperature control ATC, commonly known as the climate control system. Once you have set the target temperature, ATC system will automatically control and adjust the temperature inside the vehicle to maintain the set value automatic temperature control system Automatic temperature control system consists of a temperature sensor, a control system ECU, executive agencies. Wherein the temperature Camshaft Sensorsis a gas temperature sensor outside the car, the interior gas temperature sensor, sun sensor and an evaporator temperature sensor.
Pressure sensor / transmitter use and maintenance
Pressure sensors and transmitters are a common sensors , widely used in a variety of controlled environment, then we use the process of how to let him live longer too , today we talk in everyday life should be how to do .
1 , to prevent the waste deposited in the conduit and Crank Shaft Position Sensor with corrosive or hot media contacts .
2, the measurement of gas pressure , the pressure port should be open in the flow line to the top , and the sensor should be installed in the upper part of the process piping so that the accumulation of fluid injected into the process pipeline easily .
3, measuring fluid pressure , the pressure port should be opened in the side of the pipeline process , in order to avoid deposition of slag accumulation .
4 , guide pressure pipe should be installed in place of small fluctuations in temperature .
5 , measuring liquid pressure , Engine Temperature Sensors should be installed to avoid the impact of the liquid ( water hammer phenomenon ) , in order to avoid overvoltage damage the sensor .
6 , winter freezing occurs when the sensor is installed outdoors freezing measures must be taken to avoid the impulse in the mouth due to icing fluid volume expansion , resulting in loss of the sensor .
7, the wiring, the cable through the waterproof connector or entangling pipe and tighten the nut tight seal to prevent leakage of rainwater through the cable into the transmitter housing.
8, the measurement of steam or other high temperature medium , the need to take additional buffer tube ( coils ) and other condenser operating temperature of the sensor should not exceed the limit
1 , to prevent the waste deposited in the conduit and Crank Shaft Position Sensor with corrosive or hot media contacts .
2, the measurement of gas pressure , the pressure port should be open in the flow line to the top , and the sensor should be installed in the upper part of the process piping so that the accumulation of fluid injected into the process pipeline easily .
3, measuring fluid pressure , the pressure port should be opened in the side of the pipeline process , in order to avoid deposition of slag accumulation .
4 , guide pressure pipe should be installed in place of small fluctuations in temperature .
5 , measuring liquid pressure , Engine Temperature Sensors should be installed to avoid the impact of the liquid ( water hammer phenomenon ) , in order to avoid overvoltage damage the sensor .
6 , winter freezing occurs when the sensor is installed outdoors freezing measures must be taken to avoid the impulse in the mouth due to icing fluid volume expansion , resulting in loss of the sensor .
7, the wiring, the cable through the waterproof connector or entangling pipe and tighten the nut tight seal to prevent leakage of rainwater through the cable into the transmitter housing.
8, the measurement of steam or other high temperature medium , the need to take additional buffer tube ( coils ) and other condenser operating temperature of the sensor should not exceed the limit
Modern sensor performance requirements
With the sensor a little bit of development and progress , which involves increasingly wide range of performance requirements also change , according to the characteristics of the times and the needs of development , we will have what conditions the sensor performance to you to do a specific analysis . ( 1 ) With high-precision depth scientific research , engineering controls precise , requiring as much as possible to improve the accuracy of Camshaft Position Sensor on the "online" processing and testing requirements than 0.1μm, the rocket engine of the dynamic pressure measurement accuracy should be better than 0.1% , the microstructure of the material reaches m measurement order . ( 2 ) intelligent sensor technology to have a broad understanding of the function of the state space , the first problem is the complexity of the automation system . Such as iron and steel industry , the first control plate thickness and composition , followed by detection and management of defects on the surface shape. With the shape from the point of administration to manage the complexity of the surface , exposing sensitive devices and signal processing weaknesses. Robot appears, the more urgent requirements for intelligent Engine Coolant Temperature Sensor , there is no visual and tactile robot whose job is greatly restricted , versatility significantly reduced. Another example is the spacecraft and satellites transmit information to Earth , a huge data should first be distributed intelligent sensor processing, then compress the data transmitted to the Earth , so as to improve the efficiency of the system . Distributed processing sensor signal that is closer to human facial features , so intelligent sensors are progressive corollary ( 3 ) miniaturization and integration testing on many occasions , requires that Engine Temperature Sensors has the smallest possible size , such as onboard sensors, into the human body in biomedical sensors , wind tunnel sensors measuring the pressure field distribution , require miniaturization possible . In addition to converting the sensor miniaturization miniature components must completely apart , more importantly, the sensing element is closely associated amplifier , temperature compensation , signal storage and processing circuit must also be miniaturized . Using integrated circuit technology successfully integrated sensing elements and circuits on a single chip , so that both micro and stability is the development trend of the sensor
Use in the food storage and transportation
As food storage and transportation time is not a short-term problem , but the food stored in the relative equilibrium moisture to ensure food safety is an important indicator of the relative equilibrium moisture directly affect colony growth. To address this situation , the use of real-time monitoring of temperature and humidity Crankshaft Position Sensor temperature and humidity changes , ensure food security to enter the consumer population . When the long-distance transport or shipping refrigerated foods, how to prove that the goods have been received at the specified temperature and humidity conditions is a very important thing. Dispute resolution practice is when the shipment into the cargo hold a temperature and humidity sensor , and start it , it will faithfully record the entire transport process temperature and humidity changes , the carrier will have the responsibility to immediately known. At present, many well-known fast-food companies are using temperature and humidity sensors.
In agriculture and animal husbandry in the use of
Agriculture and livestock production , especially the production of some economic crops in their seedling stage to detailed records of temperature and humidity values . For example, to determine if certain seedling growth characteristics and the temperature, humidity , what kind of relationship , which also need temperature and humidity Cooling Temp Sensor to the data acquisition and hardship . Of course, not all need each seedling temperature monitoring , after all, is a relatively rough outline of forestry production mode .
Experiments in the use of building materials
In the building materials , especially concrete drying process, we should pay attention to the drying trend, which is one of the indicators evaluated products , but also for the construction side to provide reliable data . Application of temperature and humidity Cooling Temperature Sensor can record this data and research available to the party building , construction will provide useful help . Especially in military construction , time is life , accurately grasp the concrete drying time is starting to cause the enemy , in order to effectively provide vital forces to provide a guarantee on the battlefield , this feature can be completed by the temperature and humidity sensors .
The use of the vaccine cold chain
In vaccines, vaccine and other biological products shipped from pharmaceutical finished products warehouse , to give the populations concerned vaccination cold chain storage and transportation process , the temperature of their environment through their monitoring records , you can confirm its quality, assurance Immunization . Temperature and humidity Automobile Temperature Sensor convenient and reliable solution to this problem . Different vaccines , vaccine storage temperature for different requirements . To ensure that bacteria vaccine safety during storage and transport , storage and transportation process must be the ambient temperature in the whole process of testing records , and should be fully automated testing records , there should be no human factors , in order to improve data reliability. High-quality high-precision temperature and humidity sensors can perfectly accomplish this function , because it can be used without external power supply can also be the case for a long time record.
2013年9月13日星期五
Summary sensor in which the industry in the application
Sensor is a detection device that will convert the input variable for the measured signal is optoelectronic systems " sense organs " , is to achieve automatic detection and automatic control of the primary link . Sensor is a huge market, in 2008 the global sensor market capacity of 50.6 billion U.S. dollars , the global sensor market is expected in 2010 up to 600 billion U.S. dollars. On a global scale Crankshaft Position Sensor market is still the fastest-growing car market , is the second largest market, process control , communications, market prospects. A wide variety of Crankshaft Sensor , according to incomplete statistics , there are 30,000 kinds , pressure sensors , temperature sensors , flow sensors, level sensors have demonstrated the characteristics of a mature market , flow sensors, pressure sensors, temperature sensors largest market , respectively, accounted for the entire sensor market for 21 %, 19% and 14%. Sensor market, the main growth came from the wireless sensor , MEMS ( microelectromechanical systems ) sensors , biosensors and other emerging sensors.
A sensor in the medical device applications
One used in medical
ventilator and humidity sensors, temperature and humidity of air
transport will help to make the patient feel comfortable, when water
flow is introduced , it must be monitored and controlled.
2 is applied to the contact force sensor infusion pump to ensure delivery of liquid to the patient 's insulin pump infusion pumps and pipes unobstructed.
Three diagnostic instruments used in hospitals sensors, such as airflow sensor is used to regulate the air flow velocity gas chromatograph , contact force and position sensors automatically control laboratory robots. Pressure sensors for pump systems , the speed control of the centrifuge speed sensor , temperature sensor , the control sample and the car room temperature.
4 for gas chromatograph airflow sensor , medical chromatograph accurate monitoring and control to the gas flow . Since the ceramic sensor flow tube to avoid outgassing , which can improve the accuracy and reliability of the chromatograph .
5 for hematology analyzer infrared sensors, infrared sensors for blood cell analyzer can be used with the pump shaft encoders in combination to calculate the number of revolutions of the shaft , when the opaque object encapsulated gap hinder passage when the infrared Engine Water Temperature Sensor can detect.
6 for hematology analyzer thermistor temperature sensors used to monitor the cab , the proliferation of light and oil-cooled motor temperature to prevent overheating. If overheating , immediately shut down and allowed to cool .
7 for monitoring the instrument Ect Engine Coolant Temperature Sensor, pressure sensors, flow sensors can be used for respiratory gas monitoring, display the key indicators of breathing . Plug-in pressure sensors for monitoring blood pressure and glucose monitoring .
8 is used for anesthesia machine gas flow sensor ( referred to as the air flow sensor ) that can measure the air , the flow of oxygen and nitrous oxide , the composition of the gas supplied to the patient appropriate , in accordance with the standards set by the doctor . Thermistor temperature sensor , monitoring anesthesia machine sent air temperature / humidity, the patient can breathe comfortably , but also to avoid the inhalation of cold, dry air caused by sore throat .
9 used CPAP airflow sensor, when the patient begins to exhale, the sensor that sends signals to reduce sleep apnea machine ventilator fan speed , so patients feel and machine " confrontation" produce discomfort. Humidity sensors to monitor air humidity, dew point and accurate measurement of their absolute humidity or moisture , so that appropriate humidity of the air supplied to the patient . Three kinds of positive pressure breathing machine can apply this humidity sensor .
2 is applied to the contact force sensor infusion pump to ensure delivery of liquid to the patient 's insulin pump infusion pumps and pipes unobstructed.
Three diagnostic instruments used in hospitals sensors, such as airflow sensor is used to regulate the air flow velocity gas chromatograph , contact force and position sensors automatically control laboratory robots. Pressure sensors for pump systems , the speed control of the centrifuge speed sensor , temperature sensor , the control sample and the car room temperature.
4 for gas chromatograph airflow sensor , medical chromatograph accurate monitoring and control to the gas flow . Since the ceramic sensor flow tube to avoid outgassing , which can improve the accuracy and reliability of the chromatograph .
5 for hematology analyzer infrared sensors, infrared sensors for blood cell analyzer can be used with the pump shaft encoders in combination to calculate the number of revolutions of the shaft , when the opaque object encapsulated gap hinder passage when the infrared Engine Water Temperature Sensor can detect.
6 for hematology analyzer thermistor temperature sensors used to monitor the cab , the proliferation of light and oil-cooled motor temperature to prevent overheating. If overheating , immediately shut down and allowed to cool .
7 for monitoring the instrument Ect Engine Coolant Temperature Sensor, pressure sensors, flow sensors can be used for respiratory gas monitoring, display the key indicators of breathing . Plug-in pressure sensors for monitoring blood pressure and glucose monitoring .
8 is used for anesthesia machine gas flow sensor ( referred to as the air flow sensor ) that can measure the air , the flow of oxygen and nitrous oxide , the composition of the gas supplied to the patient appropriate , in accordance with the standards set by the doctor . Thermistor temperature sensor , monitoring anesthesia machine sent air temperature / humidity, the patient can breathe comfortably , but also to avoid the inhalation of cold, dry air caused by sore throat .
9 used CPAP airflow sensor, when the patient begins to exhale, the sensor that sends signals to reduce sleep apnea machine ventilator fan speed , so patients feel and machine " confrontation" produce discomfort. Humidity sensors to monitor air humidity, dew point and accurate measurement of their absolute humidity or moisture , so that appropriate humidity of the air supplied to the patient . Three kinds of positive pressure breathing machine can apply this humidity sensor .
Pressure up, the transmitter output falters
In such cases, you should first check the pressure connections for leaks or is blocked, if confirmation is not, check the wiring, such as the wiring is correct then check the power supply, such as the power supply is normal and then look at whether there is zero position sensor output, or look for simple pressure whether the output changes, there are changes prove Engine Temperature Sensors is not broken, if no change in the sensor that has been damaged. Other reasons for this situation may also be damage to the instrument, or other aspects of the whole system problem. Pressure transmitter output does not change, then a sudden change in pressure transmitter output, the transmitter zero relief go back. Produce this phenomenon is most likely caused by the pressure sensor ring in our customers encountered several times. General specifications reason is because the ring (too soft or too thick), Motor Position Sensor tightened, the sealing ring is compressed inside the mouth to the sensor impulse blockage sensors, pressurized pressure medium entrance, but a lot of pressure when a sudden impulse to open sealed circle, the pressure sensor under pressure and change, and the pressure is reduced again, seals and return blocked impulse mouth, no residual pressure release, the sensor zero position and get down. Exclude this reason the best way to remove the sensor directly look at the zero level is normal, if normal replace the seals and try again.
Sensor common problems and failure analysis
Sensors in the course of normal use will always fail, these failures that how to solve it, today we have common problems and Position Sensors fault analysis to expand the discussion. Use common problems are: the pressure up, the transmitter output falters pressure transmitter output does not change, then a sudden change in pressure transmitter output, the transmitter zero relief not go back. Transmitter output signal instability transmitter electrical connection with no output transducer gauge pointer control large deviation Differential Pressure Transmitter mounting position on the impact of the zero output pressure up, the transmitter output falters
2013年9月12日星期四
The problem is generally found in the sensor are the following
In the pressure sensor maintenance work , through integration of data and found that the sensor problems generally are the following : a base and a lot of oil around the plate four weeks , thus causing the insulation effect is not ideal. The gap between the base plate and the other end of the small end large, this is because Engine Temperature Sensors base of the following mill base circle , which has been subject to the impact of the role of the rolling force , no longer meet the requirements of the level when installed . Sensor is removed , the same position that it has the appearance of very severe wear , some have even been corrosion , so the force is no longer uniform . West under the indenter roll the extent of damage severe than the east , the number is also significantly more likely to analyze the results is that it may end mill drive the west , so will be rolling impact than the big east .
How to maintain the mill pressure sensor
Whatever the instrument used in a long time, the life expectancy would decline . Mill pressure sensor is no exception. Pressure sensors are very important element , which is detected when the mill rolling force , it is critical components. It is mounted on the roll , and each has one side . On the steel sheet surface by measuring the total pressure force, the detected differential pressure can truly reflect the fact on the steel sheet surface uniformity of the pressure . Because it is mounted under the roll , and the environment in which it has always been very strong vibration , humidity is very high and the temperature is high. Therefore, to maintain it becomes a very difficult thing , but expensive. Therefore, how well and how to maintain the reserve Automobile Temperature Sensor is especially important parts . Pressure sensor installation has the following technical requirements: Coolant Sensor should be installed in the roll head below the base , the above is of ninety millimeters thick are plate , and on top of it is on a 60 mm thick plate , the following part is the next fifteen millimeters thick pad . In fact , over the sensor plate with the following , both the base plate and the distance between the circumference of 1.5 mm. And there is a convex bottom base , which is embedded into the mill base inside . Both upper and lower pads, and the quality of some of the requirements of the platen . Heat treatment Hardness : HB320-360. Surface roughness of 1.6um; flatness 0.05mm; parallel is 0.05 .
The temperature sensor
Wirewound resistive temperature sensor , thermistor and thermocouple resistance of three types , their characteristics and applications has the distinction , in terms of accuracy , response characteristics and adapt to temperature and other aspects of its own characteristics. The water temperature Crankshaft Sensor Replacement, for example , its internal thermistor is a semiconductor , the lower the temperature , the greater the resistance , whereas the smaller resistance , mounted on the engine block or cylinder head of water put , in direct contact with the cooling water , which measured have the engine cooling water temperature. Electronic control unit according to this change of the measured temperature of the engine cooling water , fuel injection and ignition timing as the correction signal . Simply means that users can understand the car engine water temperature is now running the state , stop, or sports, or sports for how long .
Pressure sensor
Pressure sensors are used to detect the cylinder vacuum, atmospheric pressure , the boost ratio of the turbine engine , the cylinder pressure , oil pressure . Automotive pressure sensor applications have more capacitive, piezoresistive , differential transformer (LVDT), surface acoustic wave type (SAW). Capacitive pressure Crankshaft Position Sensor are used to detect negative pressure , hydraulic , pneumatic , measuring range 20 ~ 100kPa, with input high energy, dynamic response characteristics, environmental adaptability and other characteristics ; piezoresistive pressure sensor affected by temperature , the need separate temperature compensation circuit , but adapted for mass production ; LVDT pressure sensors have a greater output , easy digital output, but poor immunity ; SAW pressure sensor with a small size , light weight , low power consumption , high reliability, high sensitivity , high resolution, digital output , etc. , for automotive suction valve pressure detection can work stably at high temperature , is an ideal sensor .
2013年9月11日星期三
Proximity Sensor Selection Tips
Ground sensor applications has been particularly broad application of its model, different functions are also different, its main feature is the small size, easy to install, inexpensive, how do we determine what you want to do a proximity sensor to specifically look . First, the proximity sensor according to the measured object by selecting the material. If the required sensing distance is shorter, inductive proximity Engine Water Temperature Sensor can be easily and efficiently detect any type of metal objects. If the distance, you can use the photoelectric proximity sensors. If the sensor is very far away, it is best to use on the radio or reflective photoelectric sensors. Secondly, since the capacitive proximity sensor can detect the material is very much, but the sensing distance corresponding to recently, and inductive proximity sensors similar. If you use a capacitive proximity Motor Position Sensor, then the volume of the object to be detected can not be too small to meet the minimum sensing object of the sensor volume requirements. Ultrasound and diffuse proximity sensors can detect a wide range of materials, and detection distance is relatively long. However, in the detection of objects with irregular surfaces may cause problems. Finally, and more for the proximity sensor selection criteria, or to rely on the characteristics of the measured object, and to take into account the sensor installation and environmental factors. Once all these issues are clear, then it can be selected from a number of sensors a suitable type. Understanding of the proximity sensor selection step that we can more quickly and accurately selected their own needs sensors. Of course, this is just a selection procedure, to treat specific problems but also specific coping
Below these three methods work done under a brief introduction
Below these three methods work done under a brief introduction: Control explosive gas works in a sealed flameproof cabinets, full of clean gas does not contain explosive gases or inert gas, and keep the inside air pressure is slightly higher outside air pressure in the tank, the sensor is installed in the box. Type represents a positive pressure-proof method Exp.
Controlled explosion limitations works by Exd GB, Crank Position Sensors housing is designed to flameproof standard housing, instrument design standards by flameproof housing, according to stringent specifications to design, manufacture and assembly of all management approach to the implementation process, so that the the explosion of the housing seizure risk Buzhi Yu stimulate housing outer gas explosion. Explosion-proof approach to the design and manufacturing standards extremely harsh, and assembly, wiring and maintenance procedures are very strict. The approach determines the flameproof electrical equipment, instrumentation often very strict operation should power outages, etc., but many cases are also the most useful approach.Controlled detonation sourceWorks by applying barrier to isolate wiring from Positioning Sensor is processed in electricity distribution, will be supplied to the electric field sensors energy can neither be restricted enough to detonate a spark occurs, the instrument can occur exterior temperature sufficient to detonate the peace within the confines. In accordance with international norms and norms of the country, when the safe side of the gate area of the connected equipment safely attack any obstacle, the real safe way to ensure that the risk-site explosion-proof safe. Need to remind you to consider in choosing the sensor due to the use of different occasions and configuration, on-demand options intrinsically safe, explosion-proof sensors and instrumentation, but also to the supplier needs to Ex-certification.
Controlled explosion limitations works by Exd GB, Crank Position Sensors housing is designed to flameproof standard housing, instrument design standards by flameproof housing, according to stringent specifications to design, manufacture and assembly of all management approach to the implementation process, so that the the explosion of the housing seizure risk Buzhi Yu stimulate housing outer gas explosion. Explosion-proof approach to the design and manufacturing standards extremely harsh, and assembly, wiring and maintenance procedures are very strict. The approach determines the flameproof electrical equipment, instrumentation often very strict operation should power outages, etc., but many cases are also the most useful approach.Controlled detonation sourceWorks by applying barrier to isolate wiring from Positioning Sensor is processed in electricity distribution, will be supplied to the electric field sensors energy can neither be restricted enough to detonate a spark occurs, the instrument can occur exterior temperature sufficient to detonate the peace within the confines. In accordance with international norms and norms of the country, when the safe side of the gate area of the connected equipment safely attack any obstacle, the real safe way to ensure that the risk-site explosion-proof safe. Need to remind you to consider in choosing the sensor due to the use of different occasions and configuration, on-demand options intrinsically safe, explosion-proof sensors and instrumentation, but also to the supplier needs to Ex-certification.
订阅:
博文 (Atom)